Содержание
- Экструдер простыми словами
- Экструдер в пищевой промышленности
- Экструдер в фармацевтической промышленности
- Экструдер в деревообрабатывающей сфере
- Экструдер в целлюлозной промышленности
- Экструдер для пластика
- Особенности экструдера для пластика
- Одношнековые экструдеры
- Двухшнековые и многошнековые экструдеры
- Планетарные экструдеры
- Основные узлы конструкции экструдера
- Процесс экструзии
Экструдер - это что такое простыми словами
Экструдер – это механическое устройство, предназначенное для изготовления длинномерных изделий путем продавливания вязкого и пластичного материала через формующую головку. Сферы применения экструдера различны, а потому отличается формфактор устройств. Существуют универсальные модели, которые могут одновременно использоваться для выпуска нескольких видов продукции, а также специализированные устройства.
Современный промышленный экструдер – технически сложное устройство, но принцип его работы схож с работой обычной мясорубки.

Данная машина востребована в следующих областях:
- пищевая промышленность (производство макаронных изделий, крахмалсодержащей продукции, кормов);
- фармацевтика (лекарственные препараты, капсулы, упаковка);
- деревообрабатывающая промышленность (брикеты из древесных опилок);
- целлюлозное производство;
- полимерная промышленность.
Данный вид производственного оборудования также применяют в ремесленном деле: для формования заготовок, используемых в будущем в технике филигрань, имитации вязки, миллефиори. При бурении скважин, а также в металлургии тоже находит применение экструзионное оборудование.
Что такое экструдер в пищевой промышленности
Экструдер в пищевой промышленности – это устройство для непрерывного формования длинномерного изделия с последующим охлаждением и нарезкой на элементы одинаковой длины. Таким способом производят макаронные изделия, снеки и батончики, воздушные хлопья и шарики, хлебцы, кормовые добавки для животных. В пищевой промышленности используется экструзионная машина с однонаправленным вращением или двухшнековый экструдер с полным зацеплением.
При изготовлении изделий их крахмалсодержащего сырья в рабочей полости смесь прогревается до высокой температуры, приобретая гелеобразную структуру. Затем осуществляется вспенивание, в результате чего степень гелеобразования достигает 98%, а сырой жир снижается на 60-100%. На 40% повышается растворимость в воде в процессе экструзии.
Корма для животных в зерновых экструдерах изготавливают из рисовой шелухи, отрубей, яичной скорлупы, растительных добавок, крахмала, рыбной муки, сои. Экструдированная обезвоженная продукция используется для кормления рыб, цыплят, домашних животных. Срок годности готовых кормов увеличивается в несколько раз в сравнении с исходным сырьем за счет дегидратации, снижения активности патогенных бактерий и иных загрязнений.
Что такое экструдер в фармацевтической промышленности
Экструдер фармацевтический – это оборудование для непрерывного производства крупных партий лекарственных средств и стерильной упаковки (блистеров, банок, тюбиков). В данной сфере востребованы полимеры следующих видов: ПВХ, ПЭ, ПП и ПЭТ.
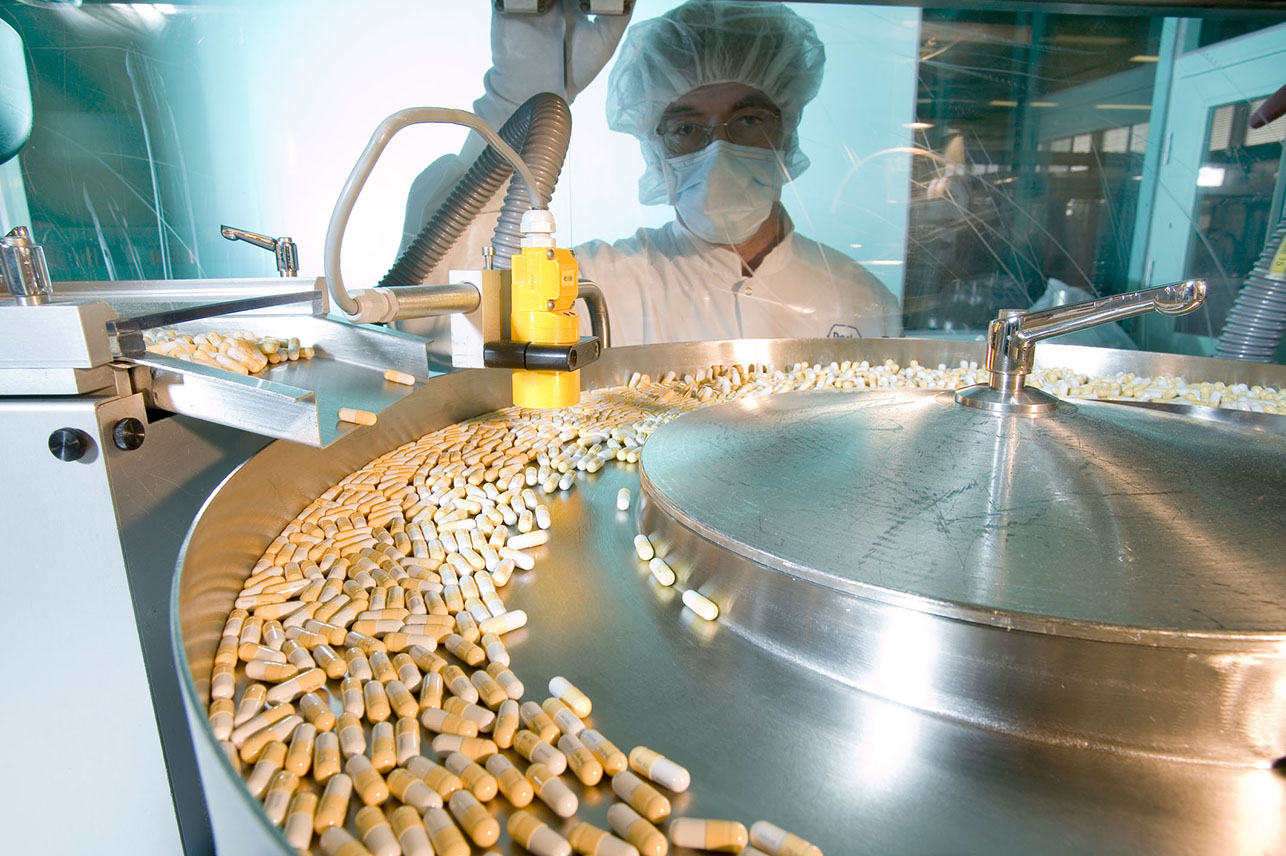
Экструдер фармацевтический может применяться в пищевой и химической промышленности. В данных сферах используют радиально-продавливающие и шнековые экструдеры. В радиально-продавливающем устройстве материал продавливается радиально и формуется, проходя через отверстия формующей головки. Отличие шнекового экструдера в том, что шнеком осуществляется одновременно вращение и возвратно-поступательное движение вдоль оси экструзии в сторону формующей головки.
В процессе экструзии происходит одновременное беспыльное смешивание компонентов на молекулярном уровне, плавление, дегазация, формование и охлаждение с последующей калибровкой. В результате достигается увеличение биодоступности ингредиентов, замедление растворимости гигроскопичных составляющих (капсул для лекарственных препаратов, пролонгированных ингредиентов). Использование фармацевтических экструдеров позволяет увеличить потенциал среднего и крупномасштабного производства аптечных препаратов.
Экструдер в деревообрабатывающей промышленности
В деревообрабатывающей промышленности экструдер – это устройство для прессования опилок с получением плотных брикетов одной формы и размера. В процессе производства изделий из дерева неизменно образуется большое количество отходов в виде опилок, которые можно использовать в дальнейшем как вторичное сырье после предварительной переработки в экструзионной машине.
Экструдер для древесных опилок имеет конический корпус с установленным внутри него коническим шнеком. Опилки подаются в питающую зону, где подхватываются шнеком и перемещаются к зоне формования. По мере перемещения они нагреваются за счет силы трения о поверхность экструдера и корпуса, от внешних нагревателей. В результате нагрева из опилок испаряется лишняя влага. Далее масса проходит через формующий канал и приобретает необходимую форму брикетов.
Что такое экструдер в целлюлозной промышленности
Простыми словами экструдер в целлюлозной промышленности – это устройство, которое помогает получать прядильные растворы целлюлозных волокон с последующим формование готовых изделий. Для этих целей используется двухвалковый экструдер, в конструкции которого предусмотрен шнековый транспортер и два ролика (подвижный и неподвижный). Для приема раствора целлюлозных волокон предусмотрен скребок шайбы, выпускная спираль и устройства накопительного типа.
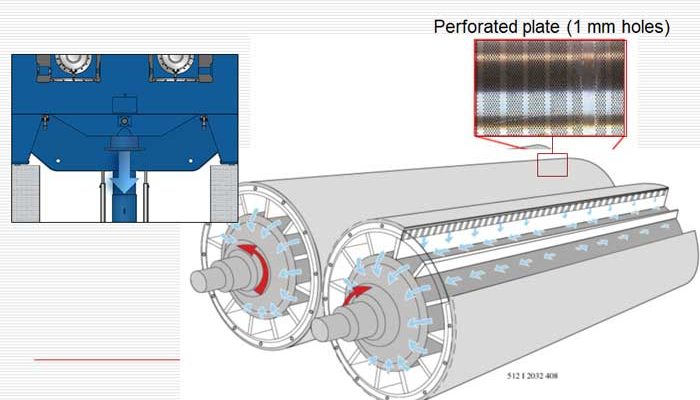
Экструдеры для производства изделий из целлюлозы могут быть установлены последовательно: на первом этапе в двухшнековом экструдере смешиваются исходные компоненты. За счет интенсивного механического воздействия замешивается однородный порошковый предраствор целлюлозы. На первой стадии используются наборные шнеки с конфигурацией, обеспечивающей измельчение и истирание компонентов при рабочей температуре не более 15°С. Более современная конструкция экструдера обеспечивает протекание всего многостадийного процесса в одном устройстве.
Экструдер для пластика - что это такое
Экструдер для пластика – это специальное устройство для изготовления бесконечно длинного изделия из полимерных и композиционных материалов. Он предназначен для переработки гранулированного сырья, дробленки, агломерата или флекса в готовую продукцию. Формование происходит за счет продавливания расплава через матрицу с последующей калибровкой. Форма калибрующего устройства (каналов матрицы, через которые проходит расплав) определяет конфигурацию будущего изделия.
Особенности экструдера для пластика
В полимерной промышленности на долю экструзионного метода приходится около половины от общего объема производства. Этим способом изготавливают изделия несложной формы без ограничения по длине. Нарезка по длине осуществляется уже после формования изделия. Потому именно эту отрасль считают основной сферой применения экструдеров различных модификаций.
Современный рынок производственного оборудования предлагает большой выбор экструдеров различного назначения. Основной критерий классификации – количество шнеков:
- одношнековые;
- двухшнековые;
- многошнековые;
- планетарные (валковые).
В зависимости от производственной мощности, заложенной в смету стоимости оборудования, и типа изделий может использоваться как самый простой одношнековый вариант, так и более эффективная модель.
Одношнековые экструдеры
Самую простую конструкцию имеет одношнековая модификация. В ней предусмотрен всего один шнек, обеспечивающий невысокую производительность. Он может выполнять радиальное или червячно-осцилирующее вращение (ЧОС).
Одношнековые модели могут быть высокоскоростными и низкоскоростными. Первые оснащаются безредукторным приводом, вторые – понижающим редукторным. Величина зазора между гребнем червяка и стенкой цилиндра зависит от диаметра шнека и определяется по формуле δ ≈ 0,01-0,015 D для низкоскоростных экструдеров, δ ≈ 0,002-0,003 D для высокоскоростных экструдеров.
Двухшнековые и многошнековые экструдеры
Двухшнековые экструдеры пользуются наибольшей популярностью. Они имеют два шнека, которые вращаются в одну сторону или навстречу друг другу. В зависимости от направления оси модели с двумя шнеками могут быть параллельными или коническими, с зацеплением или без зацепления. Двухшнековые модели обеспечивают достаточную производительность, работают с большинством полимеров.
Наиболее производительные многошнековые экструдеры. Они используются для крупномасштабного производства. Конструкция включает три шнека, два из которых вращаются в одну сторону, а третий – в противоположную.
Планетарные экструдеры
Планетарные модели экструдеров подходят для производства изделий из трудноперерабатываемых полимеров. К ним, например, относят высоконаполненные компаунды на основе ПВХ, каучук, красители порошковые. Производительность оборудования может достигать 50 тонн в час.
Планетарный экструдер конструкционно разделен на две секции: одношнековый питающий экструдер и валковый блок. Дозатор подает материал в питающую зону экструдера, откуда он передается к валкам, раскатывается тонким слоем и перемещается вперед к выходному блоку.
Валковый блок имеет центральный шнек с зубчатым зацеплением (зубцы расположены по спирали под углом 45 градусов) и несколько планетарных шнеков, вращающихся вокруг центрального. Вся система помещена внутрь материального цилиндра, шнеки приводятся в единовременное движение за счет зубчатых зацеплений. Обе секции приводятся в движение за счет трехфазного двигателя переменного тока, работающего в различных скоростных диапазонах. Выходной модуль обеспечивает формование изделия заданного сечения.
Основные узлы конструкции экструдера
Основной тип экструдера для переработки полимерных материалов – шнековый. Рассмотрим его конструкцию более подробно.
Основу экструдера составляет надежная стальная рама (станина), на которой закреплены рабочие узлы оборудования:
- редуктор и асинхронный двигатель;
- узел пластикации;
- электрошкаф управления;
- система контроля;
- система нагрева;
Над вертикальным редуктором расположен узел пластикации, который получает вращательный момент от редуктора через муфту. При вращении вала в движение приводится шнек. Сам шнек помещен внутрь корпуса, где происходит подплавление и перемешивание расплава. Поверхность шнека и корпус изнутри выполнены из инструментальной стали, устойчивой к химическому воздействию и коррозии. Шнек условно делится на несколько зон: зона подачи (загрузки), зона плавления, зона предварительного смешивания, зона дегазации (сброса газов и воздуха), зона окончательной гомогенизации и впрыска.
Наилучшего результата можно достигнуть, используя для экструзии барьерный шнек. Его особенность состоит в возможности разделения расплава и твердого исходного материала. Это достигается за счет дополнительного витка, формирующего физический барьер между двумя фазами сырья. Пропорции расплава и твердой фазы меняются в течение процесса экструзии: в начале цикла расплав занимает небольшой объем, а гранулят – основное пространство. К концу цикла соотношение меняется.
Экструдер используется для переработки термопластов, отдельных реактопластов, а также армированных пластиков с достаточным показателем текучести, компаундов. Важное условие качественной экструзии – четкий контроль температуры. На корпусе расположены кольцевые или пластинчатые нагреватели и термодатчики, обеспечивающие контролируемый нагрев каждой зоны экструдера. Большей популярностью пользуются кольцевые элементы нагрева. Точная настройка температуры на каждом участке позволяет получить более качественный расплав без риска термодеструкции полимера.
Процесс экструзии
Весь технологический процесс экструзии любого типа изделия условно можно разделить на два этапа:
- Первый этап. К нему относится экструзия с момента загрузки материала в бункер до формования. Загрузка сырья осуществляется вручную или при помощи погрузчика. Через бункер материал попадает в рабочую зону, где подхватывается шнеком, совершающим вращательное и поступательное движение. За счет этого полимерное сырье перемещается от зоны загрузки к зоне формования, одновременно подвергаясь перемешиванию, разогреву и плавлению под действием нагревателей и силы трения. В результате получается гомогенный расплав, который доставляется шнеком к формующей головке и на данном этапе полностью готов к формованию. Продавливание расплава через формующую головку выполняется под давлением. Сечения канала матрицы определяет форму будущего изделия, его толщину.
- Второй этап. Он включает постэкструзионный процесс с момента выхода сформированного изделия из матрицы до фасовки готовой продукции. В зависимости от назначения изделия может быть выполнено охлаждение, калибровка с нарезкой, сушка, аккумуляция готовых изделий в накопителе, маркировка, фасовка, упаковка и транспортировка на склад.
Второй этап может включать только охлаждение и калибровку, если изделие является заготовкой-полуфабрикатом и будет использоваться на следующем этапе производственной линии.