Содержание
Что такое агломератор
Агломератор – это оборудование для агломерации (спекания) пленочных и тонкостенных отходов при рециклинге вторичных материалов. Преимущественно используется в сфере переработки полимеров, но также оборудование востребовано в металлургии, производстве каменных композитов.
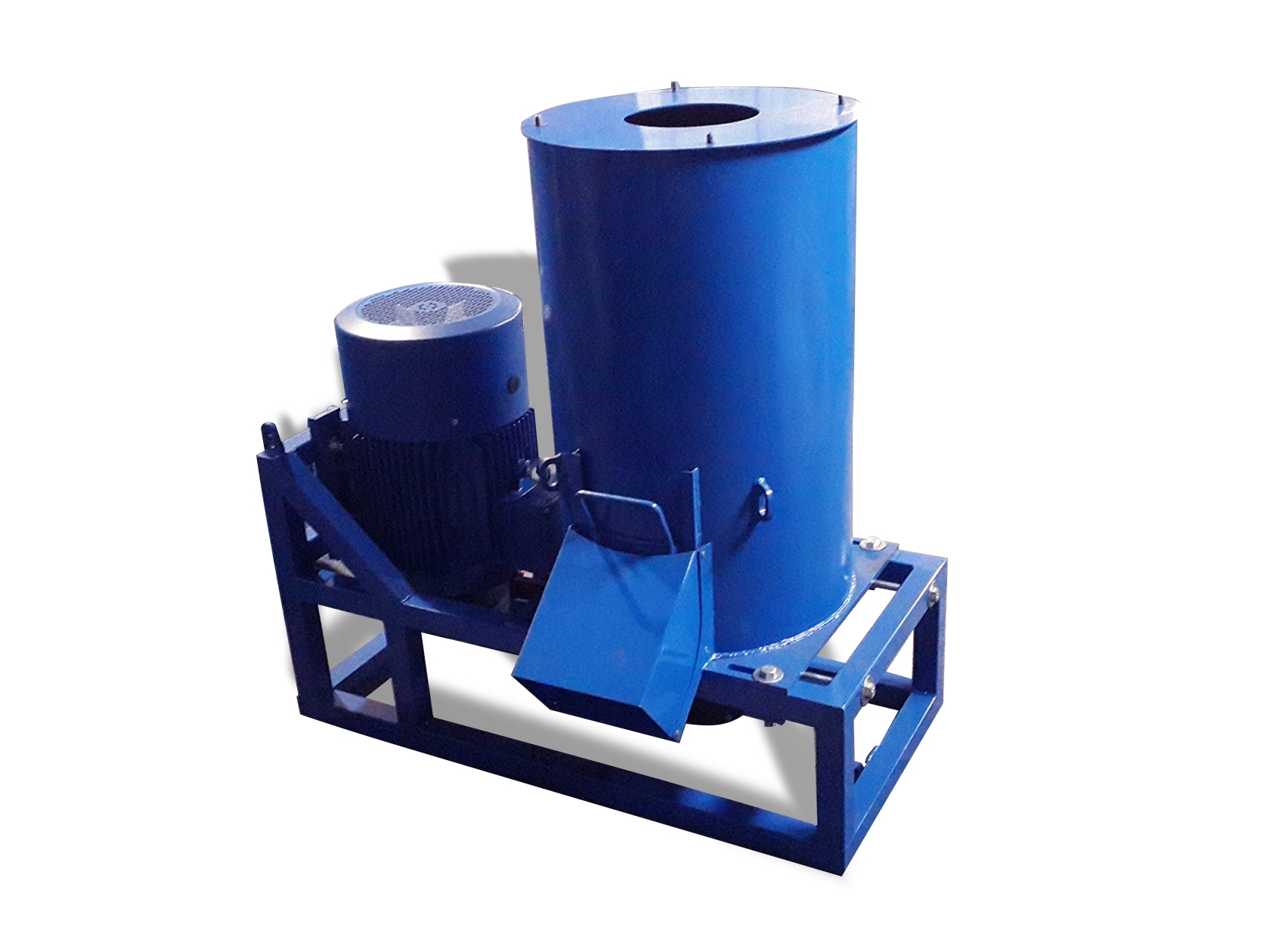
Отрасли, в которых используют агломерацию и агломераторы
Основная область применения агломератора – переработка тонкостенных и пленочных отходов пластика. В их числе:
- упаковочная и стрейч-пленка;
- производственный брак, пуско-наладочный брак;
- кромки;
- пакеты, мешки;
- сельскохозяйственная пленка, укрывной материал для теплиц и грунта.
До широкого распространения изделий из полимерных материалов агломераторы применялись в металлургии. Технология агломерирования использовалась для спекания руд цветных металлов со свинцом и цинком в составе. Принцип работы полимерных и металлургических агрегатов схож.
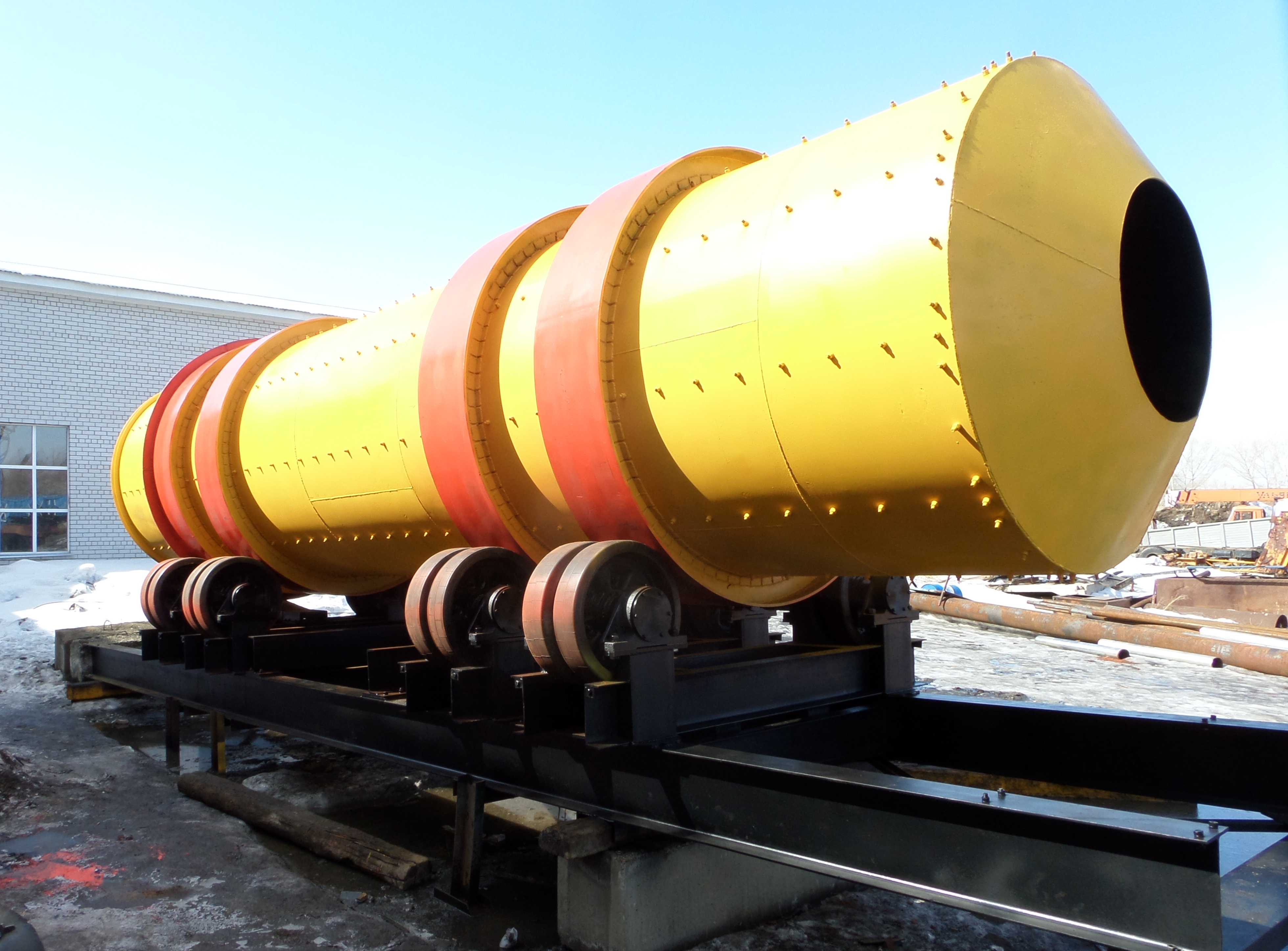
Агломерирование металлических руд – сложный технологический цикл, который требует применения различных агрегатов. В металлургии этот процесс известен как алгоритм получения кусковых фрагментов при спекании мелких фракций руды с топливом. Кусковые фрагменты далее подвергаются плавке в доменных печах.
Третье популярное направление работы агломераторов – производство каменного агломерата. На выходе можно получить пластины или плиты, состоящие из мелких фракций горных пород и полиэфирных смол в качестве связующего компонента. Каменные плиты применяются в строительстве и при ремонтных работах.
Виды агломератов в химии и металлургии
С точки зрения химии, агломерат – это совокупность частиц, соединенных прочными межмолекулярными связями. Агломераты классифицируются по структуре:
- плотные;
- рыхлые;
- луковичные.
С точки зрения металлургии агломераты бывают нескольких видов:
- с офлюсовкой (низкая степень, высокая степень);
- без офлюсовки (нефлюсованный);
- металлизированный;
- хромированный;
- фосфорный рудный концентрат;
- оксидированный;
- агломерат с самостоятельной плавкостью.

Агломерат из полимерных материалов, полученный после спекания, можно использовать в любом технологическом процессе при добавлении к основному сырью. Масса вторичного переработанного материала не должна превышать 10-30% от общего веса загруженного сырья. В отдельных технологических процессах допускается минимальное содержание вторички до 3-4%.
Типы агломераторов
Агломератор – что это такое? Это вспомогательное оборудование, которое может использоваться самостоятельно для агломерации тонкостенных отходов или в составе линии переработки. Агломераторы отличаются друг от друга конструкцией, числом роторов, мощностью, объемом камеры. Стандартные агрегаты оснащены цилиндрической камерой и прямым приводом. Также распространены варианты исполнения с клиновидной передачей, которая передает крутящий момент от двигателя к валу. Этот тип агломератора имеет меньшую высоту в сравнении с традиционным исполнением, низкую вибрационную нагрузку на привод. Однако, дополнительный механизм (клиноременная передача) требует дополнительного обслуживания.
По числу роторов агломераторы делятся на однороторные и двухроторные. Упрощенная конструкция предполагает наличие только одного ротора, заключенного в стационарный или откидной корпус. В агрегате с одним ротором перерабатывают пленочные и тонкостенные отходы мелкой и средней фракции. Агломераторы в двухроторном исполнении обладают более высокой мощностью, используется для переработки крупнофракционного сырья без предварительной сортировки и очистки в моечных комплексах.
Мощность агрегата определяет, какое количество сырья он может переработать без перегрузки и потери качества. По номинальным показателям традиционный агломератор расходует 0,2-0,3 кВт энергии на агломерирование 1 кг пушонки.
Не менее важно учитывать максимальную вместимость (объем) бака. Чем выше данный параметр, тем больше сырья можно вместить в агрегат за один технологический цикл. Объем камеры определяется произведением площади дна цилиндра и его высоты за вычетом ширины ножей. При выборе агломератора следует учитывать соответствие объема бака номинальной мощности. Увеличение вместимости за счет расширения диаметра или наращивания высоты неэффективно при сохранении тех же мощностных показателей. Крутящий момент будет меньше, что приведет к снижению линейной скорости движения частиц пушонки. Обратная ситуация, при которой увеличивают мощность с сохранением прежней вместимости цилиндра, также малоэффективна. Оборудование будет работать вхолостую, что повлечет необоснованные энергозатраты.
Конструкция агломератора
Основу конструкции агломератора составляет камера цилиндрической формы, установленная на станине – основании. В верхней части корпуса предусмотрено загрузочное окно. В боковой части бочки расположено выгрузочное окно.
Внутри бочки установлена мешалка с несколькими группами ножей по 2 в каждой. Ножи распределены равномерно по периметру камеры, что обеспечивает равномерное измельчение и перемешивание материала без слепых зон.
Для вращения мешалки, установленной на валу, крутящий момент через ременную передачу (многорядную, с фасонными зубьями, поликлиновую, узкоременную, клиновую с углом менее 40 градусов) передается от мощного асинхронного двигателя. Количество ремней варьируется от 4 до 8. Скоростью вращения двигателя составляет 1200 об/мин. Сам двигатель, как и бочка агломератора, неподвижно закреплен на станине.
Агломератор относится к оборудованию высокого класса эффективности. Средний расход электроэнергии составляет 0,22 кВт. Для стабильной работы оборудования необходимо подключить воздушный компрессор.
Технология агломерирования
Суть процесса агломерирования заключается в спекании частиц разогретого тонкостенного материала под действием шокового охлаждения. Материал предварительно измельчается в специальном оборудовании – дробилках, шредерах. За счет большого количества воздуха между фрагментами он имеет небольшой вес и большой объем.
Измельченное крупнофракционное сырье поступает в агломератор через загрузочный бункер. Количество загруженного материала определяется емкостью бункера агрегата. В агломерирующей машине пушонка дополнительно измельчается вращающимися ножами и под действием сил трения разогревается, вследствие чего испаряется лишняя влага. Сырье преобразуется в однородную расплавленную массу. Процесс измельчения и разогрева продолжается в течение 10 минут.
Интенсивное испарение влаги в бункере агломератора позволяет использовать его не только по прямому назначению, но и для сушки дробленого сырья, например, пленочных отходов в процессе рециклинга. Но на практике сушка в агломераторах используется редко по причине высоких энергозатрат, несоизмеримых с эффективностью процесса. На данном этапе технологического процесса рекомендуется использовать сушилки для соответствующего типа сырья.
На 10-й минуте оператор включает режим плавления, после чего наступает цикл отхода массы, она поднимается выше уровня ножей. Для достижения требуемой температуры сырье в бункере при агломерировании дополнительно нагревается внешними нагревателями, установленными на корпусе агрегата. Температура нагрева должна быть ниже температуры плавления, подбирается индивидуально в зависимости от типа и марки сырья.
В определенный момент времени в емкость с расплавом подается порция холодной воды, в результате происходит «шоковое» охлаждение. Расплав распадается на небольшие комки - агломераты неправильной формы размером до 2-8 мм и затвердевают. Качество сырья напрямую зависит от своевременности подачи шоковой воды агломератчиком. При преждевременной подаче охлаждающей жидкости, когда расплав не достиг требуемой температуры и гомогенности, может образоваться рыхлая масса. При задержке подачи шоковой воды появляется риск деструкции полимера, что влияет на его качество, физико-механические свойства.
Перед агломерированием следует подготовить сырье. Поскольку чаще всего исходным материалом служат полигонные, складские, производственные отходы, важно проконтролировать их чистоту и однородность, удалить все инородные частицы. По причине различных температур плавления для каждого материала за один цикл в бункер агломератора можно загружать только однотипное сырье. Инородные включения в массе могут привести к перегреву или непроплаву материала, как следствие – к низкому качеству готового агломерата.
Выгруженный из бункера агломератора комкообразный материал фасуют в мешки для последующего складского хранения или сразу отправляют на следующий этап – в гранулятор.
Агломератчик – оператор станка
Поняв, что такое агломератор, не менее важно определить, кто им управляет. В большинстве моделей предусмотрен полуавтоматический режим работы, при котором часть функций выполняет оператор станка – агломератчик. Это специалист, который настраивает, контролирует и корректирует работу оборудования для получения качественного сырья.
В профессиональные обязанности агломератчика входит:
- наблюдение за состоянием и своевременное ТО агломераторов;
- подготовка станка к ремонту при возникновении неисправностей или брака;
- включение двигателя;
- своевременная подача «шоковой» воды;
- извлечение агломерата из камеры, фасовка и маркировка.