Содержание
Грануляция что это такое простыми словами
Грануляция – это процесс преобразования сыпучего вещества в зерна-гранулы определенной формы, размера, цвета, веса, твердости. Эти зерна в совокупности называются гранулятом.
Грануляция, как правило, используется в различных сферах промышленности. В основе процесса грануляции лежит несколько процессов: диспергирование расплавов и растворов с их последующей кристаллизацией, уплотнение порошкообразной массы с использованием дополнительного связующего компонента, дробление крупных кусков (пластов, таблеток) в измельчителях до более мелких фракций, формование гранул из горячего расплава. Качество гранулята отслеживается по следующим показателям:
- Фракция, соответствующая заданному значению; однородность фракции.
- Идентичность прочности, формы, насыпной массы материала; однородность гранулометрического состава.
Грануляция не всегда обозначает процесс получения гранул. В отдельных сферах она несет в себе иное значение. Можно выделить следующие ее виды:
- солнечная грануляция;
- грануляция тканей в медицине;
- грануляция удобрений;
- грануляция в фармацевтике;
- грануляция полимерного материала.
Солнечная грануляция
Солнечная грануляция – это структура в фотосфере Солнца, формирование которой вызвано конвекцией плазмы. Если говорить простыми словами, то грануляция представляет собой яркие образования в форме гранул, которые равномерно покрывают всю поверхность фотосферы Солнца, кроме солнечных пятен.
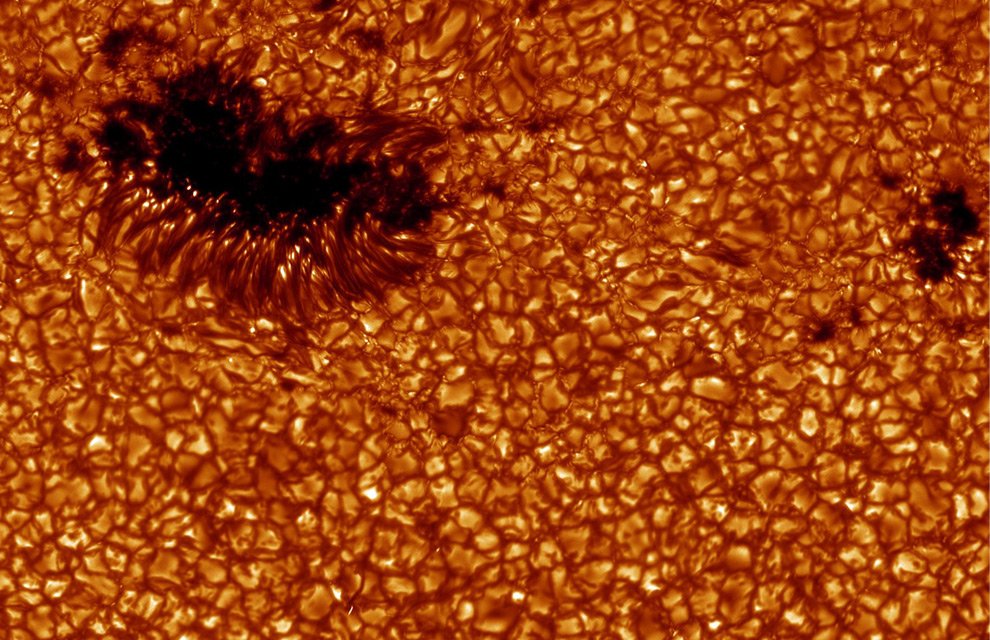
Солнечную грануляцию открыл У. Гершель еще в 1801 году, заметив через телескоп рябь на поверхности звезды. Средний размер одной гранулы 1000 км, но он может варьироваться от 250 до 2000 км. Их количество на поверхности Солнца достигает 2-4 млн. Расстояние между гранулами 300 км. Средняя продолжительность жизни обычных солнечных гранул не превышает 20 минут.
Под фотосферой находится еще один слой гранул большего диаметра – это супергранулы. Их размер достигает 30000 км. Средняя продолжительность жизни супергранул составляет 24 часа. Они постоянно возникают, меняются и исчезают.
Грануляция тканей в медицине
Грануляция в медицине простыми словами – это образовавшая при заживлении раны зернистая ткань (молодая соединительная ткань с обширной сосудистой сеткой). Грануляционную ткань впервые описал Теодор Бильрот в 19 веке. С его слов, ткань называется грануляционной благодаря своей схожести с зернами.

Грануляционная ткань имеет крупинчатую структуру, но является соединительной тканью с большим количеством коллагеновых волокон и системой капилляров. Она появляется не на всех ранах, а в том случае, когда края раны неплотно прилегают друг к другу. Примером служит грануляция на месте установки пирсинга в области уха, пупка, носа. Иногда она может образовываться в лунке на десне после удаления зуба.
Грануляция удобрений
В сельском хозяйстве процесс грануляции необходим для увеличения транспортировочной массы составов. Удобрения имеют небольшой вес при большом объеме, потому их необходимо искусственно спрессовать. Но в прессованном виде их будет неудобно применять. По этой причине предпочтение отдают методу грануляции.
Аналогичные схемы увеличения массы и уменьшения объема применяют в области первичного синтеза и переработки вторичных полимеров, в химической и фармацевтической промышленности, в пищевой отрасли.
Грануляция в фармацевтике
Существует два метода гранулирования, используемых в фармацевтической промышленности: влажная и сухая технология. Влажное гранулирование чаще используется в химической и фармацевтической промышленности, а также в пищевом производстве. Сухое гранулирование характерно для фармацевтики.
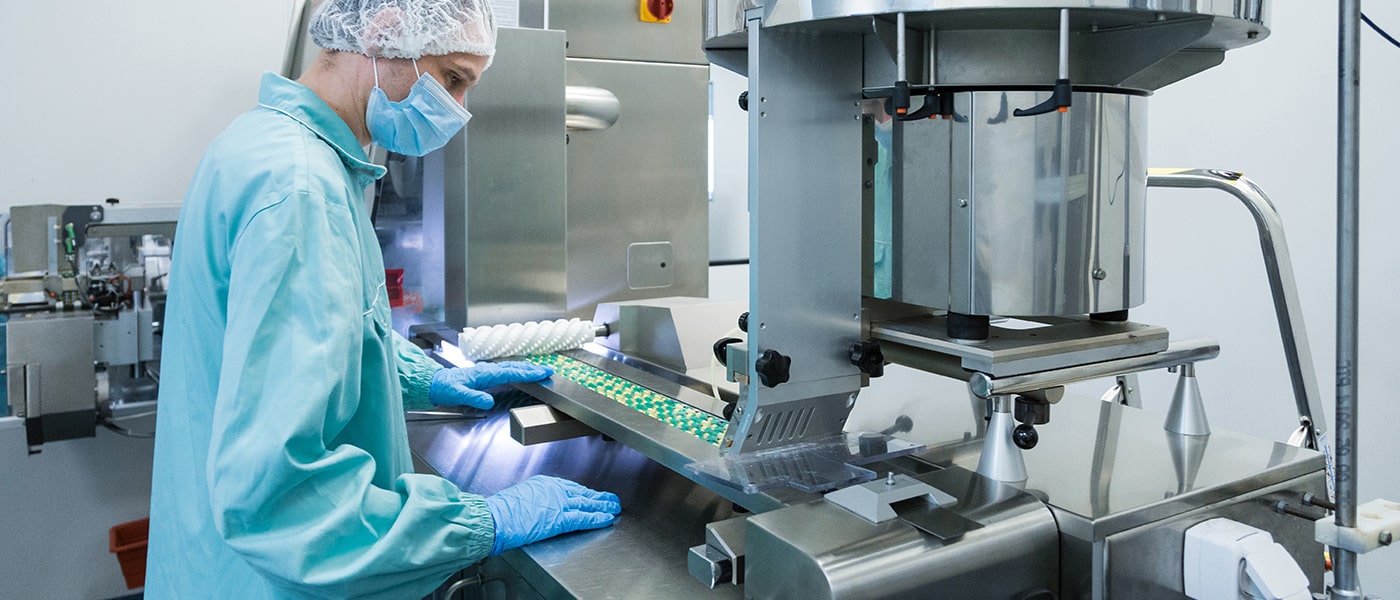
Влажное гранулирование
В процессе влажного гранулирования в порошкообразную смесь добавляют гранулирующую жидкость (жидкость-носитель). В ее состав входит растворитель с летучими свойствами, который должен испариться при высушивании. Это может быть вода, изопропанол или этанол. Возможно сочетание летучих жидкостей в разных пропорциях. Смешивание порошка с жидкостью-носителем производится в специальном грануляторе с высоким сдвиговым усилием шнеков (пример – двухшнековый гранулятор) или в грануляторе с кипящим слоем. В каждом из этих агрегатов происходит перемешивание компонентов и агрегация первичных влажных гранул из смоченного жидкостью-носителем порошка.
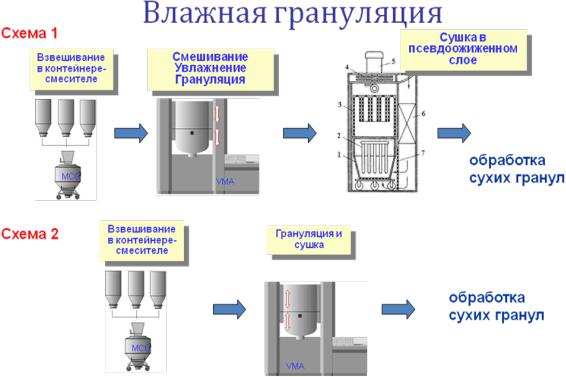
Вода в чистом виде не является надежным связующим. Она способствует образованию достаточно прочных связей между частицами порошка, но при испарении молекул жидкости связи могут разрушаться. Потому необходим раствор со связующим (клеящим компонентом), образующий более прочные соединения между частицами порошка, например, поливинилпирролидон (ПВП). Его растворяют в воде или ином растворителе с высокими летучими свойствами, а затем смешивают с порошком-основой. При соединении порошка и ПВП образуются прочные связи. В процессе высушивания вода или растворитель испаряются, между молекулами остаются только прочные связи. В результате образуется плотная масса, которая затем измельчается с образованием гранул. Также влажная масса может продавливаться через сито с образованием гранул, которые затем подвергаются сушке.
Влажная грануляция может протекать в периодическом или непрерывном режиме. Для влажного гранулирования чаще всего используется двухшнековый экструдер. В цилиндре экструдера материалы перемешиваются, а затем гранулируются под действием шнеков, продавливающих массу через сито по принципу мясорубки.
Сухое гранулирование
При сухом гранулировании используется сухое вещество без введения дополнительного жидкого раствора, поскольку материал может менять свойства при взаимодействии с жидкостью. Формирование гранул происходит под давлением путем. Основное оборудование для сухого гранулирования – таблеточная машина, валковый уплотнитель.
В таблеточной машине используют порошки, которые не обладают достаточной текучестью, потому невозможно добиться равномерной подачи материала в зону формования. В итоге масса прессуется с неравномерной плотностью.
В роликовых уплотнителях порошок подается шнеком, что обеспечивает равномерное дозирование сырья. Сырье попадает между двумя прижимными валками, уплотняется в ленту или мелкие гранулы, а затем измельчается в мельнице.

- Подача сырья в виде порошка при помощи шнекового питателя.
- Уплотнение порошка между валками. При уплотнении валки вращаются в противоположном направлении, создавая определенное давление на материал.
- Измельчение спрессованного материала в специальной мельнице с низким коэффициентом трения.
Измельчение продолжается до получения гранулята нужного размера. Затем его перемешивают и используют для формования таблетированных препаратов.
Грануляция полимеров
Самой широкой сферой применения процесса грануляции считается полимерная промышленность. Именно гранулят является основным сырьем для производства изделий из полимерных и композиционных материалов.

Простыми словами, под процессом грануляции подразумевается формование из расплава небольших гранул равного размера и формы. Для образования гранул молекулы полимера объединяются, формируя новые прочные пространственные связи.
Преимущества грануляции
Грануляция – предсказуемый и многократно повторяемый процесс, результатом которого является гранулят стабильного качества (при условии правильной настройки оборудования и смешивания компонентов в соответствии с заданной рецептурой). Основным оборудованием для грануляции полимеров является гранулирующий экструдер. Он обеспечивает высокую производительность: 50-100 кг/ч для простых одношнековых моделей, 3-20 т/ч для многошнековых высокопроизводительных моделей.

Грануляция позволяет решить проблему сегрегации инертных материалов – концентрацию более мелких и плотных частиц в нижней части емкости, а легких и крупных – в верхней части. Это снижает текучесть массы при пересыпании. Гранулы же имеют правильную равномерную форму и одинаковый размер, потому сегрегация в гранулированной массе не возникает.
Некоторые порошкообразные материалы бывает сложно спрессовать даже при условии добавления в смесь уплотняющего компонента (клея). Но те же самые материалы в виде гранулята уплотняются намного проще. Мелкие частицы необходимо подвергать уплотнению дольше, чем более крупные частицы. При этом плотноспрессованную таблетку с постоянной твердостью все равно не получится изготовить. Грануляция позволяет решить эту проблемы.
После гранулирования материал занимает меньший объем при той же массе. Это свойство особенно важно при транспортировке и при подаче сырья в загрузочный бункер. Легкие и объемные материалы не позволяют использовать производственное оборудование на полную мощность, что приводит к неоправданным энергозатратам.
Конструкция гранулятора
Гранулятор – механическое устройство, состоящее из станины и размещенных на ней основных рабочих узлов, а также вспомогательных устройств. К числу основных узлов гранулятора относятся:
- Загрузочный бункер. Это металлический бак, обеспечивающий подачу сырья извне в питающую зону экструдера. Бак может иметь круглую, квадратную, многогранную форму сечения. Независимо от формы, размер нижней части загрузочного бункера всегда меньше размера верхней его части. Это необходимо для равномерной подачи сырья.
- Шнек. Это основной рабочий орган гранулятора. Тип шнека во многом определяет тип перерабатываемого полимера, производительность устройства, скорость технологического процесса, равномерность и качество смешивания. В грануляторе может быть установлен один (одношнековый), два (двухшнековый) и более (многошнековый) винтовых вала. Шаг нарезки, форма шнека, направление вращения также имеют важное значение. Шнек условно разделен на несколько зон: загрузки (питания), пластификации, дегазации (опционально), смешивания и гомогенизации, повторной дегазации (опционально), формования.
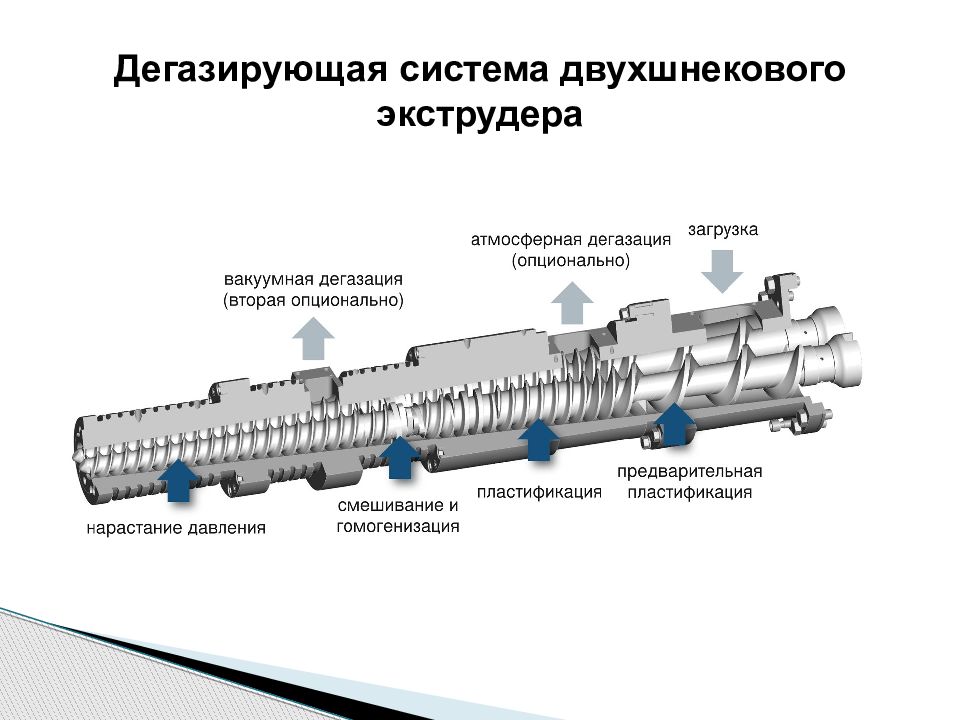
- Цилиндр. Это корпус устройства, внутри которого расположен шнек. Внутри цилиндра протекают все основные процессы подготовки полимера к грануляции. Он изготовлен из химически устойчивой и термоустойчивой ткани, выдерживает длительные температурные и механические нагрузки.
- Двигатель. Электродвигатель обеспечивает вращение вала с заданной скоростью.
- Нагреватели. В грануляторах используются нагреватели хомутового или полухомутового типа, которые крепятся снаружи на корпусе. Внутри цилиндра могут точечно использоваться пальчиковые нагреватели, которые выполнены из износостойкого материала и выдерживают воздействие полимерных материалов с различными химическими добавками. В паре с термодатчиками нагреватели обеспечивают нагрев до требуемой температуры без разрушения полимера.
- Система охлаждения. Для охлаждения стренгов (стержней) используют воздушную, водную или смешанную систему охлаждения. Эффективность той или иной системы зависит от выбранной технологии гранулирования и от типа полимера.
- Система ножей. Ножи, изготовленные из инструментальной стали, могут работать как с холодными, так и с горячими стренгами. Ножи вращаются с заданной скоростью, выполняя при этом нарезку прутка.
- Фильтры. Фильтрация важна при переработке вторичных материалов. Если на этапе измельчения и промывки материал в дробленке остаются грязевые включения, они оседают на фильтрах. Чаще это песок, металлическая стружка, волокнистые вкрапления. Фильтры необходимо периодически очищать, чтобы сохранить установленную производительность гранулятора.
- Формующая головка. Формование изделий осуществляется через формующие каналы в матрице гранулятора. Форма и диаметр калибровочного канала определяет форму и размер будущего изделия.
Грануляция осуществляется в непрерывном режиме. На выходе можно получить гранулы заданного размера, цвета, формы.
Технология грануляции полимерных материалов
Грануляции можно подвергать как первичные полимер в виде порошка, так и вторичку в виде флекса, пушонки или дробленки. Все эти материалы в дальнейшем успешно используются в процессе производства изделий из полимерных материалов методов вакуумного формования, экструзии, литья под давлением, прессования.
С порошкообразной первичкой можно работать сразу в грануляторе. Вторичку необходимо подготовить: отсортировать для извлечения инородных включений, промыть до получения чистого пластикового полуфабриката без гразевых примесей, которые могут сказаться на качестве готового гранулята, затем измельчить, просушить до требуемого уровня гигроскопичности и отправить в гранулятор.
Порошок или иной сыпучий материал подают в цилиндр гранулятора через загрузочный бункер. Он попадает в питающую зону, откуда подхватывается шнеком и перемещаются к зоне формования. В процессе перемещения материал нагревается за счет силы трения и за счет нагревателей, которые установлены на корпусе. Пластиковая масса постепенно переходит в вязкотекучее состояние и перемешивается. Вместе с основным полимерным веществом в гранулятор могут добавляться красители, пластификаторы, стабилизаторы и иные компоненты. Все составляющие смеси перемешиваются до однородной массы и нагревается до температуры, обеспечивающей достаточную текучесть при формовании, но не достигающей температуры деструкции. Температура нагрева зависит от типа полимера. По этой причине не смешиваются разные полимерные материалы в одном технологическом цикле.
Расплав, достигший зоны формования, уже находится в вязкотекучем и гомогенном состоянии. Он продавливается через формующую головку, имеющую несколько равноразмерных каналов. Диаметр канала определяет диаметр будущей гранулы. Расплав под давлением продавливается через каналы матрицы и формуется в длинные стержни. Далее осуществляется охлаждение и нарезка стержня на отдельные гранулы. Нарезка осуществляется пластинчатыми или дисковыми ножами, которые расположены непосредственно на выходе из фильеры и прилегают к ее плоскости. При вращении ножей стержень режется на небольшие элементы – гранулы. Шаг нарезки зависит от скорости вращения ножей, может быть меньше или больше. Гранулы охлаждаются воздухом или водой. Возможно формирование стержней с водяным охлаждением, последующей нарезкой на гранулы и просушкой. Порядок постформовочных операций определяет классификацию грануляции по типу резки: с холодной стренговой резкой, с горячей водокольцевой резкой, с горячей воздушной резкой, с подводной резкой. Сушка гранулята является завершающей операцией грануляции.

Готовый материал фасуется, маркируется и отправляется на склад или на следующую стадию переработки. Вторичное сырье используется как добавка к первичному с целью снижения себестоимости и изменения физико-химических свойств готового изделия.