Содержание
- Проектирование дробилки
- Разработка проекта
- Конструирование дробилки для пластика
- Инструменты и материалы
- Выбор конфигурации и материала для корпуса
- Выбор вала под ножи
- Выбор материала и конфигурации ножей
- Выбор подшипниковых узлов
- Выбор электромотора для дробилки пластика
- Выбор материалов для рамы
- Выбор типа бункера
- Пошаговая инструкция по конструированию
- Советы по обслуживанию измельчителя
- Частые вопросы
Развитие полимерной отрасли неизбежно способствует увеличению объема пластиковых отходов. Помимо всем привычных производственных (брака, облоя, литников) и бытовых отходов (бутылки, канистры, иная тара, пакеты, пленки) активно развивается печать на принтерах ЗD, вносящая свой вклад в общий объем пластикового мусора. Потому так важно своевременно утилизировать поддающиеся переработке виды полимеров, чтобы избежать экологической катастрофы.
Источник фото https://www.stankoff.ru/blog/post/364
Чаще сборка дробилка своими руками интересна начинающим предпринимателям и молодым конструкторам. Но, не имея чертежей и общего представления, придется все разрабатывать с нуля. Процесс сбора конструирования и сборки дробилки своими руками займет в этом случае немало времени. Чтобы ускорить процесс, расскажем, что необходимо для изготовления измельчителя в условиях любого подсобного помещения.
Проектирование дробилки для пластика своими руками
Конструирование любого изделия начинается с проектирования или поиска прототипа. Профессиональные чертежи шредеров или дробилок (они отличаются друг от друга только фракцией материала на выходе, понятия часто используются как синонимы) найти в свободном доступе сложно. Ни одна компания, выпускающая измельчители, не заинтересована в обнародовании чертежей. В рамках данной статьи приведем примерные схемы конструирования, списки необходимых материалов и инструментов.
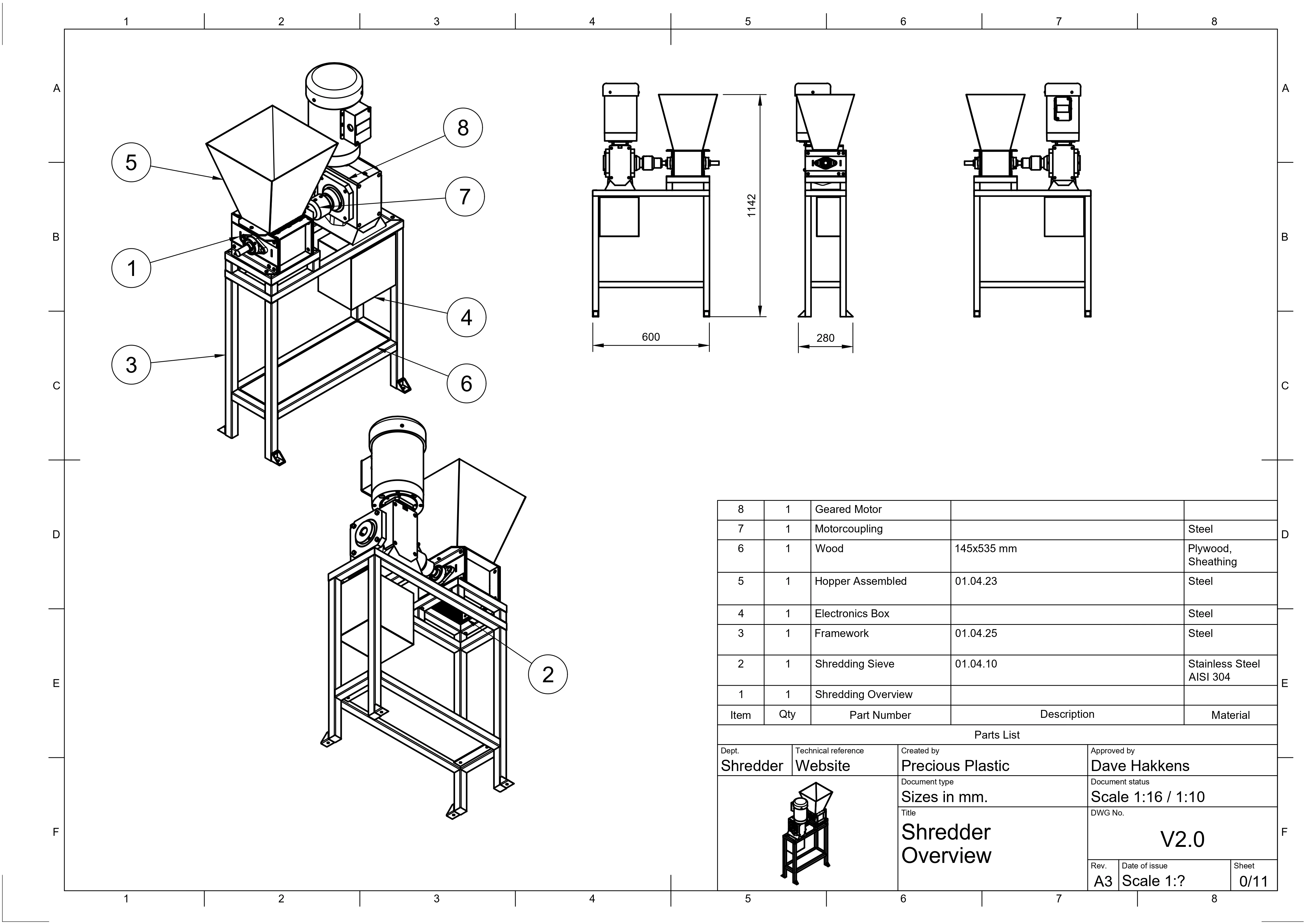
Еще один вариант сконструировать дробилку без чертежей – использовать имеющийся прототип. Часто в продаже можно найти неработающие устройства, которые продают за символическую плату. Но не всегда есть возможность разобрать прототип для детального изучения, выполнения замеров и составления чертежей.
Исходные данные для конструирования измельчителя
Прежде всего, следует определиться, с какими отходами и в каком количестве планируется работа. Учитывая тип материала, подбирают ножи; учитывая объем переработки, рассчитывают габариты корпуса и мощность двигателя. Основные характеристики, на которые следует обратить внимание:
- мощность двигателя;
- размер бункера подачи сырья;
- диаметр валов, их количество;
- конфигурация ножей.
Расчет требуемой мощности вручную – процесс трудоемкий и требующий определенных технических знаний. В этом случае как раз пригодится прототип, опираясь на характеристики которого проще будет определить требуемую мощность, вместительность и количество валов. Для промышленных дробилок в карточках товаров производители указывают основные характеристики, на которые также можно опираться при выборе двигателя, вала, подшипников, ножей.
Разработка проекта
Большая часть начинающих конструкторов, которые впервые проектируют и собирают дробилку своими руками, отдают предпочтение версиям мини-формата. Для создания такого оборудования не требуется использовать сложные инструменты и дорогие материалы.
Под проектированием дробилки понимается следующий алгоритм действий:
- расчет и выбор мощности двигателя;
- выбор редуктора с требуемым передаточным числом;
- расчет параметров вала;
- расчет объема загрузочного бункера;
- расчет грузоподъемности подшипников;
- разработка чертежей.
В качестве основы для измельчителя можно использовать болгарку, безударную мощную дрель или перфоратор. Для конструирования измельчителя используется приводной механизм выбранного устройства с двигателем. Однако упрощенные версии данных инструментов с уменьшенной мощностью использовать при конструировании дробилки не рекомендуется. В связи с недостаточной мощностью двигатель при рабочей нагрузке быстро выйдет из строя.
Конструирование дробилки для пластика
Дробилка имеет достаточно простую конструкцию. Основное направление применения дробилок – измельчение материала до требуемой фракции. Потому в конструкции должен быть блок ножей, бункер для загрузки, корпус, в котором будет осуществляться измельчение (статор), вращающийся вал для ножей (ротор) и двигатель, обеспечивающие движение ротора. Тип ножей зависит от того, какие расходы необходимо будет перерабатывать. Для мягких полимеров, нейлона, акрилового пластика, АВС используют V-образные ножи. Для твердых видов пластика, включая ПЭТФ-тару, применяют острые зубчатые ножи, закрепленные на роторных валах. Крупногабаритные изделия типа оконных рам из ПВХ, корпусов техники, ящиков можно измельчать в конусных, щековых или молотковых дробилках.
В данной статье рассмотрим, как сделать роторную одновальную дробилку своими руками. Она оптимальна для измельчения наиболее объемного класса отходов – канистр, бутылок, малогабаритной тары, фрагментов труб малого диаметра. Конструкция может иметь один или два вала, но чаще встречаются схемы именно одновальных самодельных роторных измельчителей. Они проще в сборке и обслуживании, дешевле.
Следует учитывать, что не всегда дробилка, сконструированная самостоятельно, обходится дешевле б/у измельчителя. Потому необходимо предварительно рассмотреть несколько вариантов и оценить предстоящие расходы. Если выбор все же падет на самостоятельную сборку измельчителя, первый экземпляр лучше собирать из доступных и не самых дорогих материалов, поскольку велик риск необоснованных расходов.
Инструменты и материалы
Для того чтобы собрать дробилку с нуля, потребуются перечисленные ниже материалы, а также метчик, набор отверток или шуроповерт, крепежные элементы, сварочный аппарат, измерительные инструменты. При самостоятельном раскрое металла потребуется болгарка.
Материалы и узлы, необходимые для конструирования дробилки:
- листы нержавеющей стали (марка AISI 304) толщиной 3, 5 или 6 мм для корпуса;
- лист стали для бункера толщиной 1 мм;
- стальная труба нужного диаметра (сталь марок 40, 45, 40Х) для расточки вала;
- 2 подшипника (диаметр зависит от диаметра вала);
- блок подвижных ножей из рессорных (65Г, 60С2, 65С2ВА) или штамповых (Х12МФ) сталей;
- неподвижные ножи (08Х18Н10);
- сетка с ячейками требуемого размера для калибровки измельченного материала;
- квадрат-труба для рамы;
- двигатель мощностью 2 л/с с редуктором;
- переключатель прямого/обратного хода.
Самодельную дробилку лучше проектировал с разборным корпусом на болтовых соединениях. Это значительно упростит процесс технического обслуживания, замену ротора и его составных частей в случае необходимости.
Выбор конфигурации и материала для корпуса
Раскрой листов проще и безопаснее выполнять на лазерном станке. В этом случае точность раскроя будет выше, а стыки герметичнее, чем при самостоятельной резке. Лазерная резка выполняется по точным чертежам, их необходимо разработать заранее или доработать под свои задачи те, что получится найти в свободном доступе. Раскроенные детали могут иметь незначительное количество окалин.
Далее требуется выполнить ряд токарных работ, нарезать резьбу при помощи метчика в тех местах, где предусмотрены болтовые соединения. После раскроя и нарезки резьбы рекомендуется отшлифовать все детали для более точной стыковки, используя гриндер или наждачную бумагу. При отсутствии гриндера придется потратить немного больше времени на ручную шлифовку наждачной бумагой, набитой на брусок для удобства, но пропускать этот шаг не рекомендуется. Любые недочеты и неровности приведут к неправильной стыковке деталей, перекосу конструкции.
Для скрепления деталей корпуса используется сварка. Прочный и надежный сварной шов выдерживает длительные и интенсивные эксплуатационные нагрузки. Отдельные элементы фиксируются болтовыми соединениями.
В качестве корпуса можно использовать отрезок трубы большого диаметра (400-500 мм), выполнив в нем лючки для загрузки сырья в верхней части, для выгрузки сырья в нижней части, для крепления вала по бокам. Если трубы нет, корпус собирают из листов толщиной 3 мм, 5 мм или 6 мм. Двигатель следует установить на безопасном расстоянии от ножей.
Для получения материала произвольной фракции никаких дополнительных манипуляций с выходным отверстием не производят. Если необходимо получить строго определенную фракцию, в нижней части устанавливается фракционная (калибрующая) решетка с ячейками требуемого диаметра. Под сеткой или выходным отверстием устанавливается емкость для сбора измельченного пластика: контейнер, мешок.
После шлифовки каркаса его следует покрыть любым лакокрасочным материалом, который предотвратить коррозию. Покрытие наносится только с внешней стороны, внутри корпуса под действием перемещающихся кусков материала краска быстро сотрется.
Выбор вала под ножи
Вал служит основой конструкции ротора. Валы предпочтительнее изготавливать из закаленной стали, выдерживающей значительные нагрузки. За основу берут круглый прокат и растачивают под требуемые размеры. В качестве недорогой альтернативы подойдет стальная труба диаметром 20 или 25 мм из конструкционных сталей 45 или 40Х.
Заводские валы уже расточены на концах, что обеспечивает надежную посадку подшипников. Покупка заводского вала упростит процесс сборки дробилки своими руками.
Выбор материала и конфигурации ножей
Ножи изготавливают из инструментальной стали.
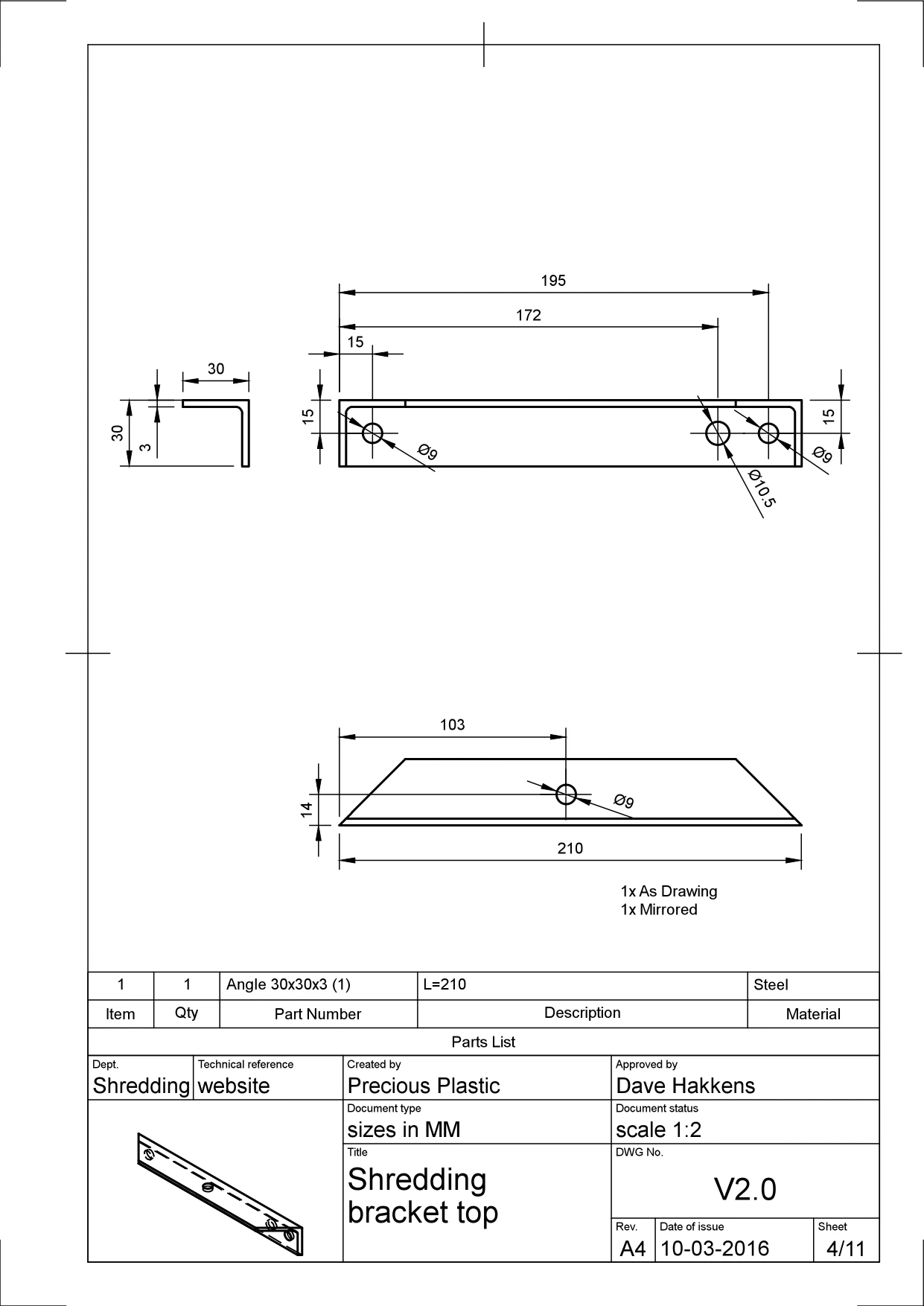
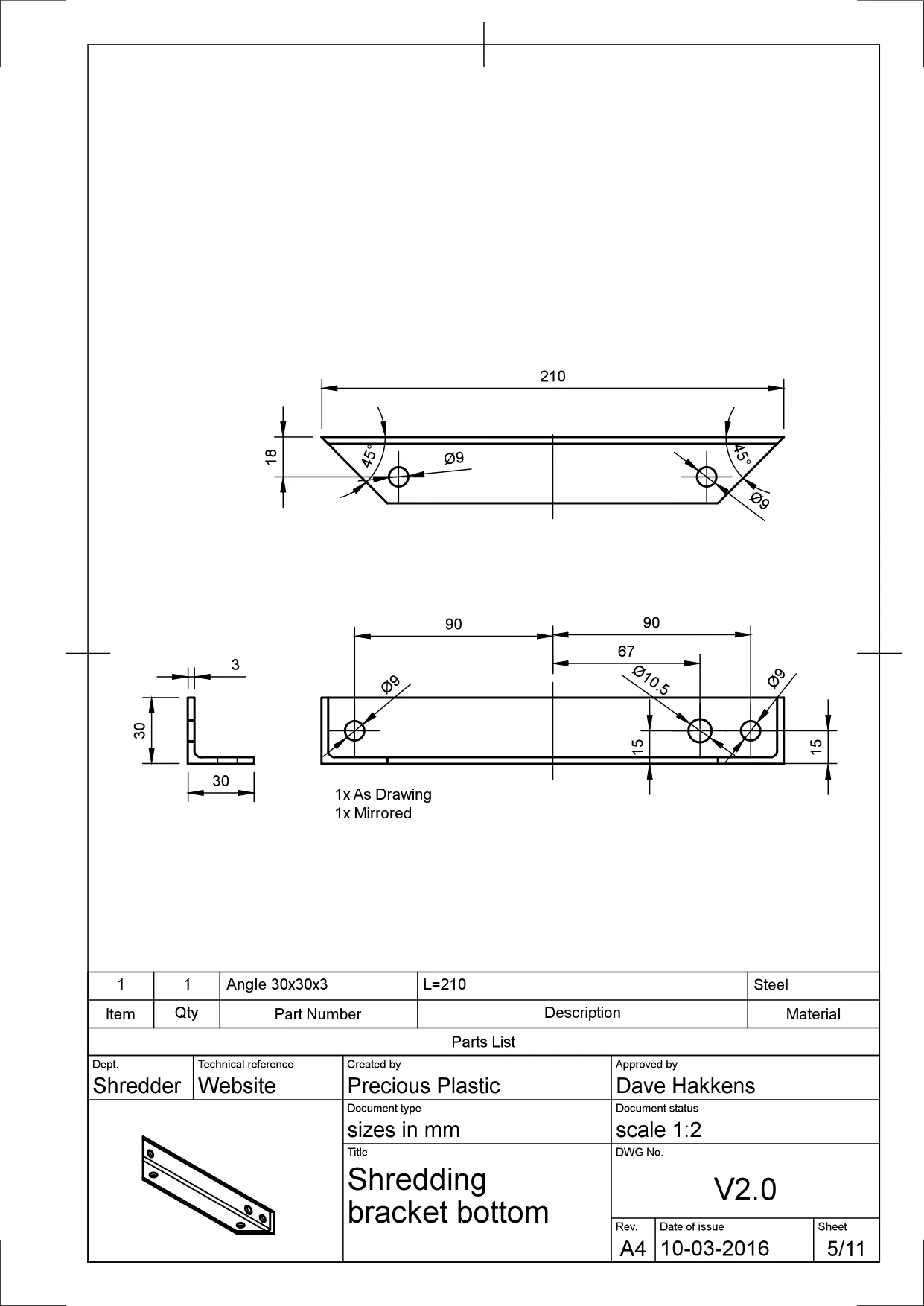
Предварительно заточенные ножи собирают на оси вала, чередуя с шайбами до тех пор, пока вал полностью не заполнится. В итоге ножи образуют спиралевидный блок. На боковую стенку монтируются (привариваются или вставляются в пазы) неподвижные ножи. После установки вращающихся и неподвижных ножей следует проверить, что при вращении они не цепляют друг друга. При заклинивании ножей конструкцию рекомендуется разобрать и собрать повторно, исключив зазоры и перекосы.
Источник фото https://www.stankoff.ru/blog/post/364
Ножи можно заказать специально под дробилку по имеющимся чертежам, а можно использовать лезвия от дисковой пилы. Потребуется 15-20 дисковых лезвий. Устанавливать диски необходимо также с небольшим смещением относительно друг друга по оси. Между дисками выдерживается расстояние в несколько миллиметров (на помощь снова приходят шайбы).
Выбор подшипниковых узлов
Наиболее экономичный вариант для дробилки своими руками – радиальные подшипники. Но важно соблюсти соосность, в противном случае вал перекосится, будет возникать перегрев основных узлов.
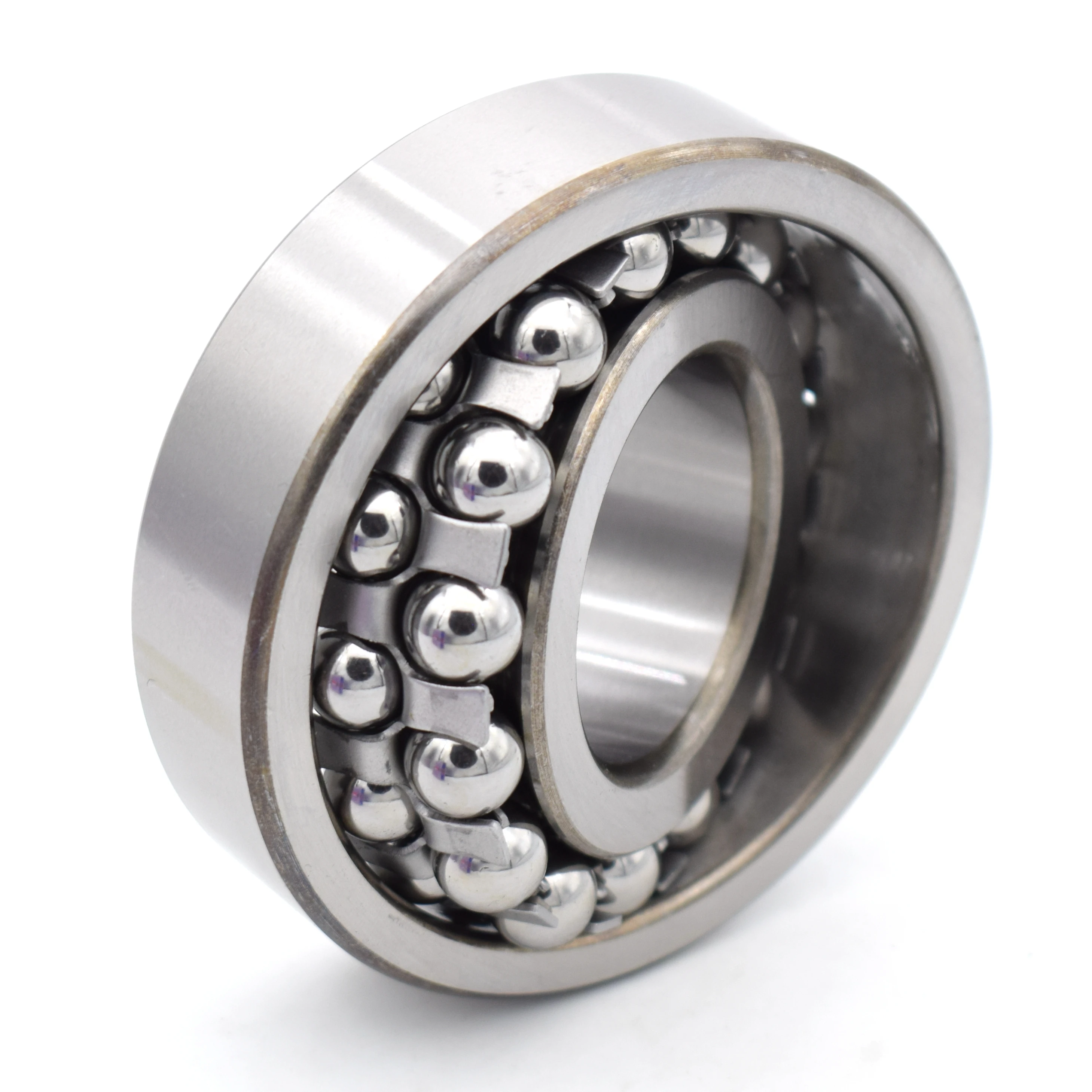
Более дорогие, но менее чувствительные к перекосу самоустанавливающиеся подшипники обеспечивают работу узла и передачу крутящего момента даже при незначительном перекосе без разрушения. Можно использовать более износостойкие двухрядные сферические подшипники, если самоустанавливающиеся по каким-либо причинам поставить нет возможности. Однако они отличаются меньшей точностью и скоростью вращения.
Выбор электромотора для дробилки пластика
Двигатель необходим для приведения в движение вала измельчителя. При выборе привода можно рассмотреть несколько вариантов: электромотор, двигатель внутреннего сгорания, ручная тяга. И перечисленных вариантов предпочтительнее электропривод. Минимальные требования к двигателю – мощность 2 л/с, число оборотов 1400 об/мин; к редуктору – 70 об/мин.
Электродвигатель должен передавать крутящий момент к редуктору через ременную передачу или муфту. Ременная передача - не самый надежный способ, при застревании пластика ремень может слететь или разорваться. Однако это самый экономичный и бесшумный вариант, обеспечивающий плавный ход с небольшой потерей КПД. В случае использования муфты потери КПД отсутствуют, габариты привода меньше, но стоимость соединения через муфту выше.
Выбор материалов для рамы
Рама или база - основа конструкции. На ней крепятся все основные узлы и корпус измельчителя. Базу рекомендуется изготавливать из квадрат-трубы с сечением 40Х40. При конструировании рамы не следует ее сильно завышать, конструкция будет менее устойчивой. Средние размеры базы 100Х50 см, высота 80 см. Крепление измельчителя к базе осуществляется при помощи уголков методом сварки.
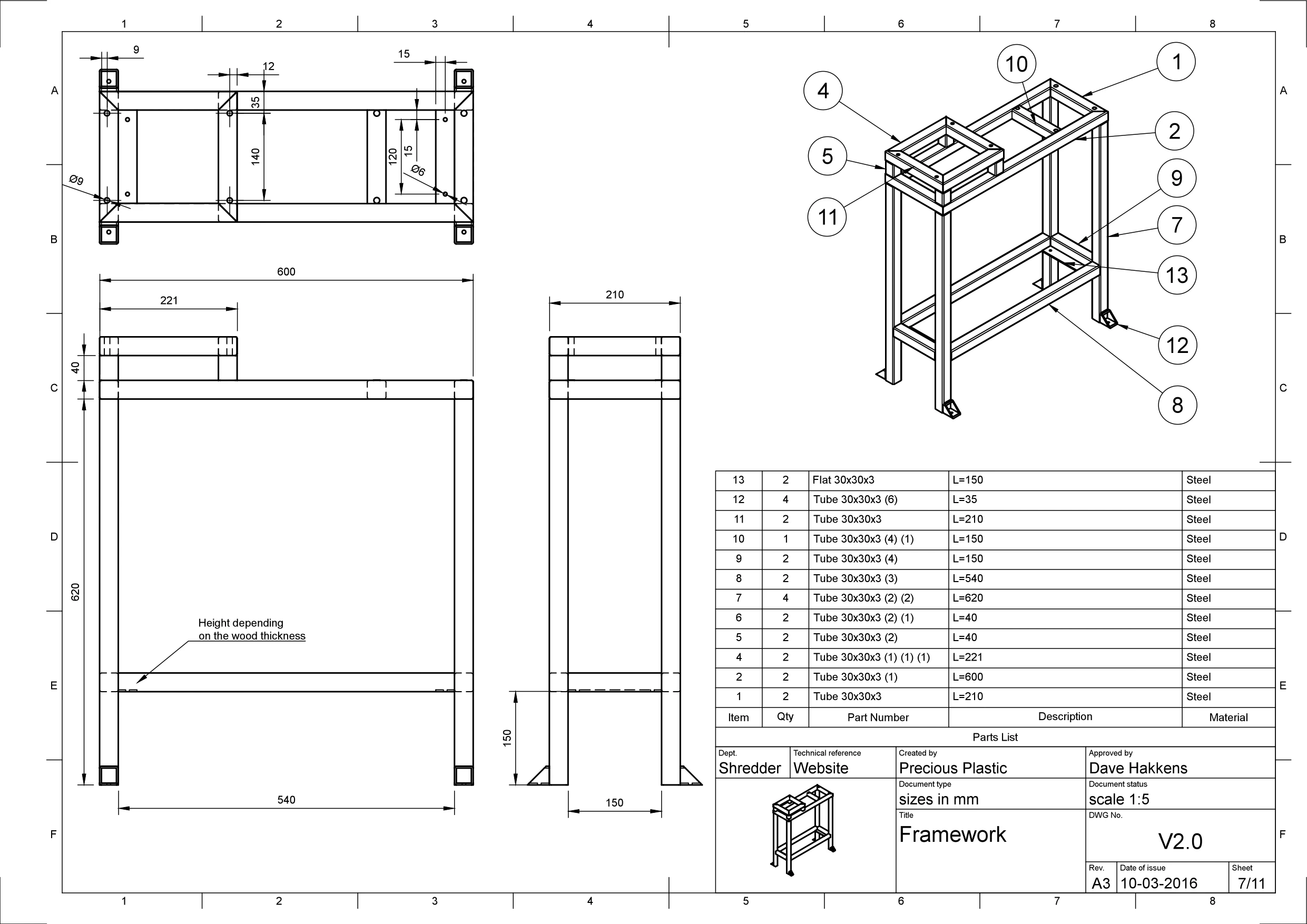
В связи с достаточно большим весом измельчителя рекомендуется его устанавливать на колесную раму. Это обеспечит мобильность устройству.
Выбор типа бункера
Загрузочный бункер должен соответствовать объему измельчителя. Чрезмерно большой бункер не нужен, он будет утяжелять конструкцию. При недостаточном размере бункера возможно снижение производительности и работа вхолостую из-за недостаточной подачи материала.
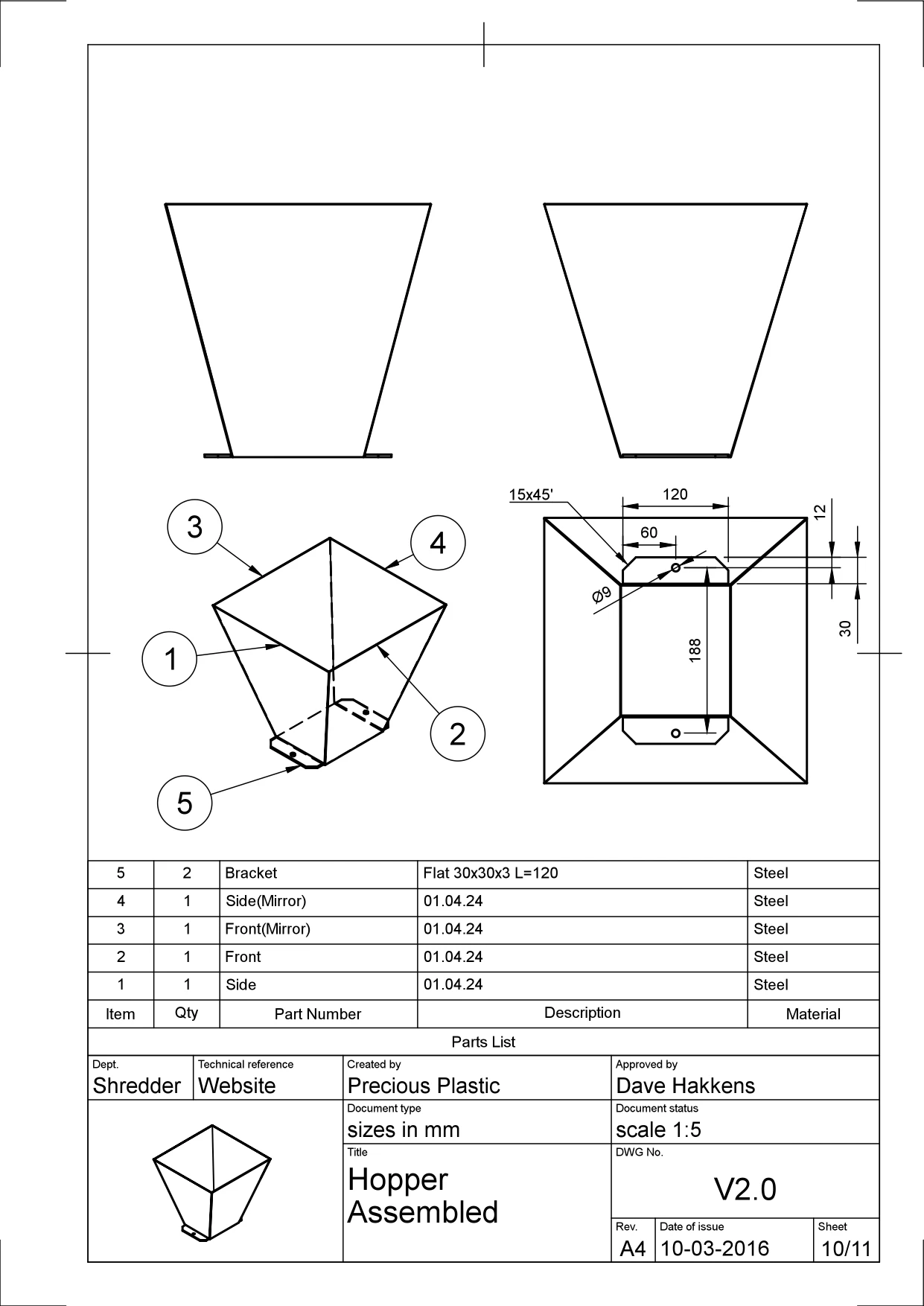
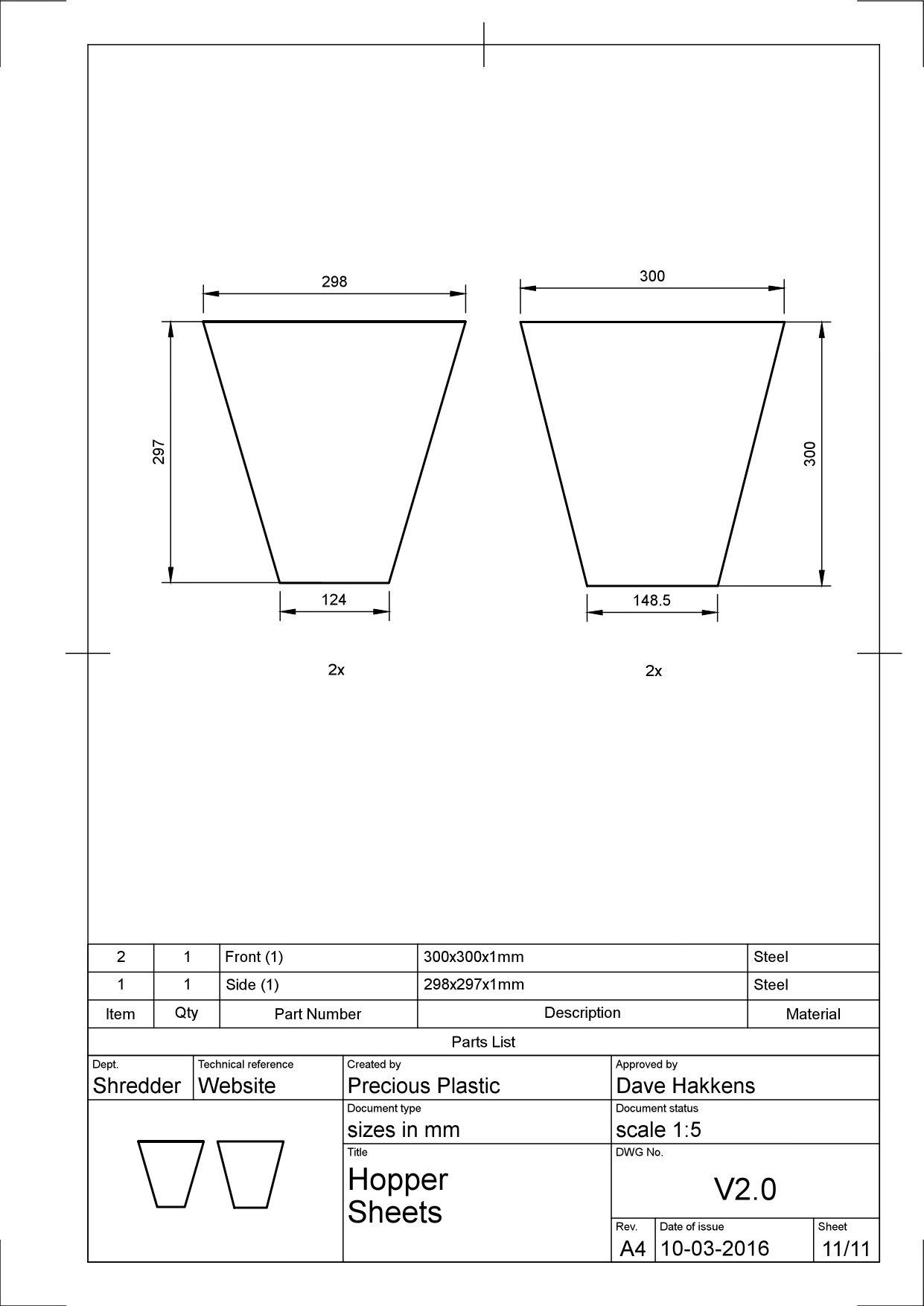
В некоторых случаях необходимо обеспечить принудительную подачу сырья с небольшим давлением. Для этой цели подойдет загрузочный бункер с квадратным сечением, в который буде входить толкатель аналогичного размера и сечения. Его можно изготовить из стального листа толщиной 1 мм методом сварки.
Пошаговая инструкция по конструированию
Первый этап – сборка корпуса. При сборке используют сварку и болтовые соединения. Перед сборкой необходимо проверить чистоту и качество деталей. Они должны иметь ровный срез и отшлифованную поверхность. Особое внимание следует уделить целостности вала, ротора и подшипников. Эти детали подвергаются наибольшему износу в процессе эксплуатации измельчителя.
Второй этап – установка лезвий на оси, чередуя ножи и шайбы. При сборке элементов режущего блока следует выбирать ножи равного размера (диаметра) с одинаковым количеством зубьев. Шайбы обеспечивают требуемый технологический зазор, в который при вращении входят неподвижные ножи. Шайбы также не дают дискам смещаться по оси и сливаться воедино.
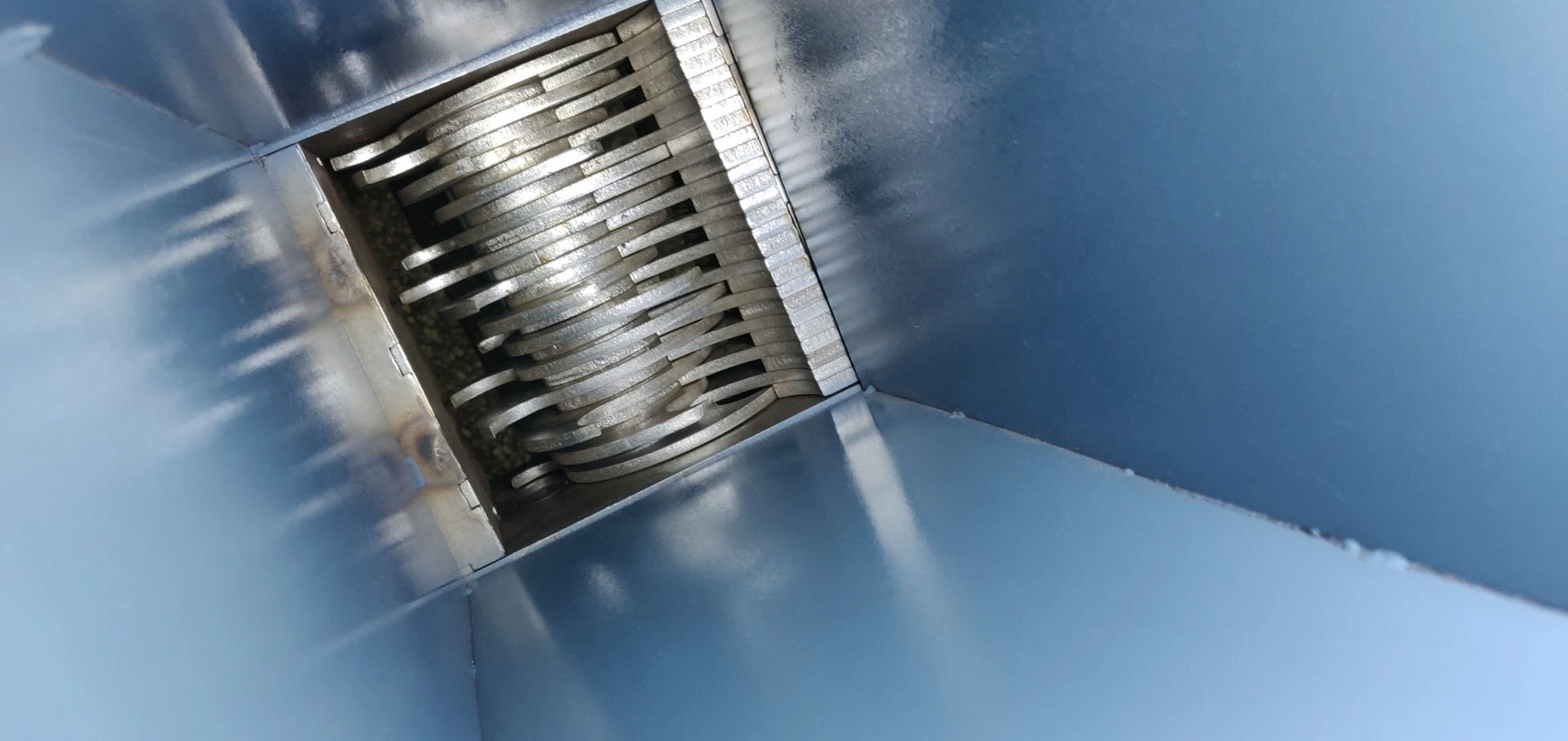
Третий этап – установка неподвижных ножей на боковой стенке. Неподвижные ножи необходимы для очистки подвижных лезвий от налипшего пластика и для дополнительного измельчения. При конструировании двухвального шредера неподвижные ножи чаще всего не требуются.
Четвертый этап – установка подшипников и вала в корпус будущего измельчителя. Важно обеспечить плотную посадку подшипников на концах вала. Для этого используют дополнительные шайбы или прокладки.
Пятый этап – сборка базы из труб квадратного сечения. Рама может быть разборной или сварной. Второй вариант надежнее, потому предпочтительнее.
Источник фото https://www.stankoff.ru/blog/post/364
Шестой этап – монтаж корпуса измельчителя с валом и мотора на раму, соединение загрузочного бункера и системы выгрузки сырья с корпусом при помощи сварки. После сваривания и скрепления через разъемные соединения всех элементов конструкций можно переходить к подключению двигателя. Подключение вала к электромотору осуществляется через муфту или ременную передачу.
Советы по обслуживанию измельчителя
Любое оборудование подвергается износу в ходе эксплуатации. При обслуживании дробилки может требоваться периодическая заточка ножей. Для этого необходимо демонтировать ножи, предварительно обесточив двигатель. Если ножи изготовлены из качественной инструментальной быстрорежущей стали, они подвергаются многократной заточке. Регулярное обслуживание двигателя – еще один важный момент. Необходимо очищать и смазывать подшипники, что обеспечит плавность хода вала и стабильность работы всего узла.
При работе устройства следует останавливать двигатель и делать перерыв через 30 минут эксплуатации. При непрерывной работе в течение длительного времени возникает перегрев двигателя, возрастает износ щеток при их наличии, перегревается обмотка, может возникнуть межвитковое замыкание, которое в итоге приведет к поломке двигателя.
Эксплуатация дробилок, сделанных своими руками, должна осуществляться с заземлением или с занулением (минимальное требование). Это важно условие безопасной эксплуатации оборудования.