Содержание
Шредер – это устройство для первичной фрагментации материала. Оно имеет максимально простую конструкцию, в зависимости от типа измельчаемого материала может использоваться на первой или последующих стадиях фрагментирования.
Шредер - что это такое простыми словами
В переводе на русский язык «shredder» означает «измельчитель», «уничтожитель». Сферы применения и потребители шредеров разнообразны:
- офисы;
- банки;
- архивы;
- производственные предприятия;
- правительственные организации;
- частные лица.
В зависимости от области использования отличаются и типы шредеров:
- для бумаги;
- для камня;
- для металла и металлолома;
- для пластика.
Все категории шредеров имеют схожую конструкцию. Это электрические устройства, оснащенные приемным бункером и системой ножей. Они отличаются размером и выходной фракцией материала:
- Шредеры-плоскорезы. Они оснащены вращающимися ножами, которые способны фрагментировать материал на узкие полоски с сохранением исходной длины изделия. Этот шредер создает небольшой объем расходов, применяется в личных целях, в офисах для уничтожения старых и ненужных документов. Данные могут быть восстановлены.
- Шредер-конфетти. В конструкции предусмотрено два барабана, которые из первоначального листа вырезают ромбы, квадраты или прямоугольники, постепенно измельчая его. Применяются в тех же целях, что и предыдущие. Данные могут быть восстановлены.
- Шредеры-крошители. Измельчители работают по принципу конфетти-шредеров, но вырезают либо прямоугольные, либо круглые фрагменты из исходного листа.
- Шредеры-резаки. Подходят для измельчения неплотной бумаги, рвут листы с помощью вращающихся ножей.
- Шредеры-грануляторы и дезинтеграторы. Устройства многократно измельчают лист до тех пор, пока фрагменты не будут проходит через калибровочную сетку. Размер частиц минимален, восстановление данных затруднительно.
- Шредеры-шлифмашины. В конструкции предусмотрен вращающийся вал с ножами, которые измельчают лист до тех пор, пока фрагменты не станут достаточно маленькими для прохождения через нижний калибрующий экран.
- Промышленные шредеры. Используются для измельчения любых материалов. Внутренняя режущая система зависит от того, какое сырье подвергается переработке. Они рассчитаны на массовое измельчение макулатуры, древесины, резины, кожи, автомобильных покрышек, плитки или камня, металлических изделий.
В качестве альтернативы режущим шредерам можно назвать те, которые уничтожают лист методом поджога, компостирования, химического разложения. Они не используются в частном порядке, чаще востребованы в производственных зданиях и правительственных учреждениях.
Что такое шредер для пластика
Шредер – измельчающее промышленное оборудование, обеспечивающее первичную фрагментацию материала (резку, дробление, раздавливание). Шредеры применяются для измельчения бытовых и производственных отходов пластика, картона, дерева, металла, каменно-рудных материалов, стекла, текстиля, синтетических волокнистых материалов. Они имеют простую конструкцию и простой принцип работы. При правильном выборе модели по параметрам можно добиться качественного измельчения с минимальными затратами на закупку оборудования.
Как выглядит шредер:
Для чего нужен шредер
Измельчение в шредере – первый этап переработки изделий, имеющих высокий показатель сопротивления разрушению. Шредеры используются для труб, крупногабаритных листов и панелей, автомобильных бамперов, садовой мебели, литых элементов, слитков, ящиков, смешанного строительного мусора, грунта. Средняя фракция фрагментов переработанных изделий составляет 15-100 мм. Для получения сырья более мелкой фракции требуются дополнительное оборудование – дробилки, мельницы.
В полимерной промышленности, в сфере деревообработки, переработки макулатуры, стекла после шредера материал подвергается дополнительному измельчению в дробилке до фракции 6-10 мм. Полимерное сырье далее может использоваться для переработки в грануляторах с целью получения гранулята – вторичного производственного сырья с частицами одной формы и размера. Стеклянный бой, целлюлозное сырье, металл также успешно подвергаются вторичной переработке.
Важно учитывать, что универсальным для различных типов материалов считается только четырехвальный шредер. Также в промышленности применяются двухвальные и одновальные шредерные измельчители, имеющие узкую область применения. Двухвальные модели подходят для резки шин, тары из полиэтилентерефталата. Паллеты можно разрушать в одновальных измельчителях.
Устройство шредера
Промышленные измельчители используется перерабатывающими предприятиями, специализирующимися на рециклинге твердых бытовых отходов, брака и технологического лома. Шредеры имеют простую конструкцию: на стальной неподвижной станине установлен привод, приводящий во вращение роторные валы. Сами роторы заключены в металлический корпус с загрузочным окном в верхней части и фракционной решеткой в нижней части. Станина крепится к фундаменту, потому станок остается неподвижным даже при серьезных вибрационных нагрузках. Для снижения вибрационной нагрузки могут опционально использоваться виброопоры. Они получили распространение в шредерах для КБО.
Материал, направленный на измельчение, подается в рабочее пространство через загрузочный бункер (загрузочное окно). В маломощных и среднемощных моделях загрузочные бункеры изготовлены из пластика. Для крупногабаритных мощных шредеров бункер загрузки изготавливают из металла, что продлевает срок службы агрегата и его отдельных узлов. Дробильное оборудование работает под контролем оператора. Загрузка сырья в бункер осуществляется вручную, при помощи пневматического питателя или иного транспортирующего устройства. Сырьем служат цельные изделия и их фрагменты, помещенные в загрузочный бункер поштучно или группами.
Через загрузочное окно перерабатываемый материал попадает в рабочее пространство шредера внутри корпуса. Корпус выполнен из износостойкой стали. В нем расположены роторные валы. Их количество зависит от модели оборудования. Валы изготавливаются из стали, имеют гладкую износостойкую поверхность, устойчивую к истирающим нагрузкам. На роторных валах размещены остро заточенные ножи (лезвия), обеспечивающие резку материала. Ножи дискового типа крепятся на валах при помощи винтовых соединений, их можно демонтировать в случае затупления. Для одновальных конструкций ножи чаще выполняются несъемными. Затупившиеся лезвия демонтируются вместе с валом для заточки. При вращении валов ножи движутся, соприкасаются с лезвиями других роторов и неподвижными ножами, расположенными на корпусе. При этом лезвия дробят отходы любого типа на более мелкие фрагменты.
По ходу перемещения материала в рабочем пространстве возможно возникновение заторов или уплотнений, препятствующих свободному движению сырья. Для улучшения качества измельчения и увеличения производительности в одновальных шредерах используется фидер (толкатель, подпрессовщик). Фидер – это плита с собственным гидравлическим или пневматическим приводом, которая с определенным усилием давит на измельчаемый материал. Сила воздействия плиты на массу сырья зависит от уровня сопротивляемости материала и определяется автономно. При достижении максимально допустимого значения движение плиты прекращается. Это также необходимо для предотвращения перегрузок, преждевременного износа и повреждения валов. В многороторных устройствах подпрессовщик не используется.
Одновальные и двухвальные шредеры: какому отдать предпочтение
При выборе оптимальной модели шредера следует обратить внимание на следующие основные характеристики:
- диаметр ротора (зависит от размера разрушаемого изделия);
- мощность двигателя;
- число оборотов роторного вала (низкоскоростные, высокоскоростные);
- размер фракционного сита;
- производительность оборудования.
Диаметр ротора или каждого из роторов (для многовального оборудования) подбирается в зависимости от перерабатываемого материала. Диаметр вала в маломощных моделях составляет 100-200 мм. При средней мощности оборудования диаметр может достигать 200-400 мм. Мощные и сверхмощные агрегаты оснащаются роторами диаметром от 400 мм. Крупногабаритные отходы перерабатывают на роторах диаметром 480 мм и выше.
Двигатель приводит в движение ротор. Потому от его характеристик зависит общая производительность агрегата. Одновальные роторы способны показывать мощность до 200 кВт, двухвальные – до 220 кВт. Такой мощности достаточно для измельчения среднегабаритных тонкостенных и толстостенных отходов. Оборудование тяжелого класса для КБО характеризуется мощностью до 440 кВт и наиболее высокой производительностью.
Число оборотов ротора (частота вращения вала) определяет скорость работы оборудования. Чем меньше размер и толщина стенки изделия, тем выше может быть скорость его переработки. Для крупногабаритных и толстостенных отходов рационально использовать низкоскоростные роторные шредеры.
Фракционное сито определяет степень измельчения. В характеристиках оборудования указывается диаметр ячейки, который варьируется в диапазоне 15-150 мм. Проходящие через калибрующую решетку фрагменты материала попадают в накопитель, более крупные частицы повторно подвергаются дроблению. Возможно использование шредера без калибрующей решетки. В этом случае выполняется один цикл дробления заданной продолжительности. Результатом такого измельчение станут фрагменты материала разного размера и формы. Данный режим работы подходит для предварительного дробления.
Производительность – один из важных параметров выбора оборудования, зависящий от перечисленных характеристик (мощность, количество и диаметры валов, число оборотов, габариты отходов). По производительности можно судить, сколько килограмм сырья получится переработать за один час на данной модели оборудования. В среднем при измельчении на стандартном оборудовании можно получить от 300-500 кг/ч и более материала.
Отличие процесса измельчения для однороторного и многороторного шредера
Процесс измельчения материалов в однороторном и двухроторном шредере имеет незначительные отличия. Они обусловлены определенными конструктивными особенностями и устройством.
При наличии одного ротора с закрепленными на нем ножами дублирующие неподвижные ножи размещаются на корпусе. Между ними образуется рабочее пространство, куда падает изделие или его крупные фрагменты из бункера. При вращении ротора подвижный дисковый нож попадает в зазор между неподвижными лезвиями, разрубая и раздавливая находящийся там материал. Одновальный шредер работает на низкой или средней скорости. Для улучшения производительности предусмотрена подпрессовка материала фидером. Гидравлическая плита одновременно двигает материал в сторону ротора и сжимает тонкостенные изделия, ломая их. Сила воздействия фидера на материал регулируется автономно. Движение плиты останавливается в тот момент, когда сила сдавливания достигает максимальной величины. После этого плита возвращается в исходное положение, а материал продолжает измельчаться до более мелких частей в рабочем пространстве за счет движения ножей. Цикл измельчения повторяется многократно в течение установленного оператором времени или до момента, пока все фрагменты материала не пройдут через калибрующую решетку.
В многороторном шредере предусмотрено два и более вала. Остро заточенные ножи, закрепленные на соседних роторах, образуют рабочую область. При запуске двигателя и начале движении валов один дисковый нож входит в пространство между двумя лезвиями, закрепленными на соседнем роторе и вращающимися во встречном направлении. Возможна дополнительная установка неподвижных ножей на корпусе, что улучшает качество дробления. Неподвижные ножи также выполняют функцию скребков и удаляют с подвижных лезвий налипший материал. Валы вращаются с невысокой скоростью, благодаря чему материал постепенно измельчается без нагрева. Работа устройства протекает в относительно бесшумном режиме без образования облака пыли в помещении.
Какой шредер выбрать: однороторный или двухроторный
Выбор типа измельчителя зависит от условий его использования. Наиболее мощные четырехроторные шредеры применяются на больших предприятиях, где перерабатываются ЖБИ, изделия с металлической арматурой, крупногабаритные отходы, бочки и канистры большого объема.
Четырехвальное оборудование имеет два основных и два дополнительных ротора, благодаря чему достигается высокая степень дробления. Они вращаются синхронно попарно во встречном направлении. Нижние роторы являются основными, расположенные над ними – вспомогательными. Ножи закреплены на всех четырех валах и дополнительно оснащены захватывающими крюками. В связи с увеличенной мощностью значительно возрастает стоимость оборудования с четырьмя роторами и расходы на его обслуживание, потому оно менее востребовано в среднем и малом перерабатывающем бизнесе.
Наибольшее распространение получили одновальные и двухвальные роторы. Они менее универсальны, имеют среднюю мощность, но более доступную стоимость. Отдельные модели этого типа оборудования могут иметь мобильный тип исполнения, что делает возможным их применение в малом бизнесе и в быту. Для удобства перемещения мобильные шредеры оснащают рамой с колесами или монтируют на автомобильном шасси. В большинстве случаев и одновальные, и двухвальные шредеры имеют более надежную стационарную конструкцию, устанавливаются без перемещения в составе перерабатывающей линии или автономно.
Основное отличие однороторных и двухроторных моделей в степени измельчения и типе перерабатываемых материалов. Одновальные устройства позволяют получить материал размером 100-150 мм (крупная фракция) или 25-100 мм (средняя фракция). В двухроторных моделях можно получить сырье как вышеперечисленных фракций, так и мелкого помола (10-25 мм).
Для переработки твердого пластика, литых и прессованных изделий, а также дерева (веток, досок, щепы), стекла можно использовать однороторные шредеры. Они привлекательны низкой ценой, малым потреблением энергии, возможностью установки в составе производственной линии. К недостаткам стоит отнести невозможность переработки волокнистых, вязких, эластичных материалов, упругих полимеров, пленочных изделий, бумаги, тонкостенной тары.
Двухвальные шредеры за счет асинхронно вращающихся роторных валов с закрепленными лезвиями и дополнительных ножей, размещенных на корпусе, измельчают тонкостенную тару, емкости, резиновые изделия, упругие полимеры, автомобильные шины после предварительной резки на гильотине. В двухвальном шредере отсутствует подпрессовщик, материал затягивается между валками и режется ножами. Для более надежного захвата ножи оснащаются крюками. Скорость вращения валов низкая, потому измельчение осуществляется равномерно, без сильного шума и образования пылевого облака. Преимуществом двухвальной конструкции является быстрое и качественное измельчение в сравнении с однороторными моделями, однако стоимость оборудования выше.
Выбор между одновальным и двухвальным шредером должен осуществляться в зависимости от типа перерабатываемых материалов, объема твердых отходов, имеющегося бюджета. Для предприятия среднего масштаба оптимально приобрести двухвальный шредер. Он характеризуется универсальной сферой применения (полимеры, пленка, ПЭТ-тара, канистры, стекло, архивы, макулатура, кости, медицинские отходы, дерево, металл, ветошь, кабельная продукция, литники). Имеет среднюю производительность от 600 кг/час, измельчает материал до фракции 10-100 мм.
Пример как работает шредер
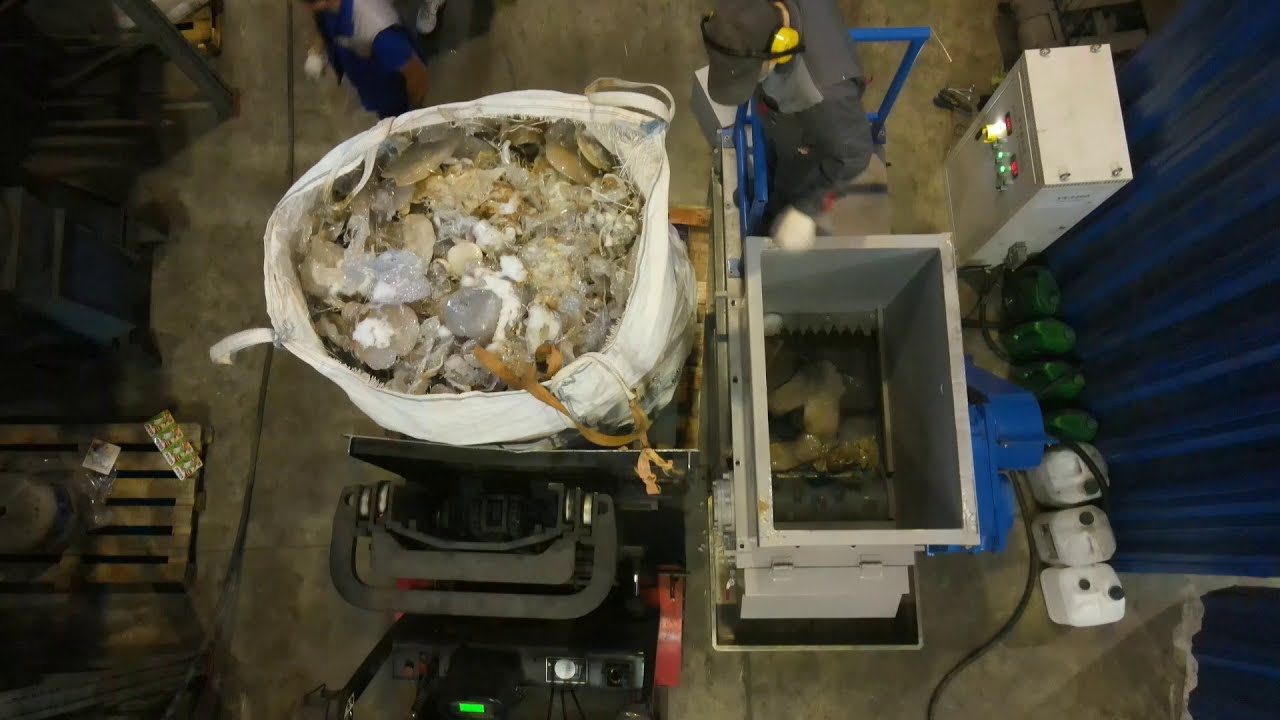
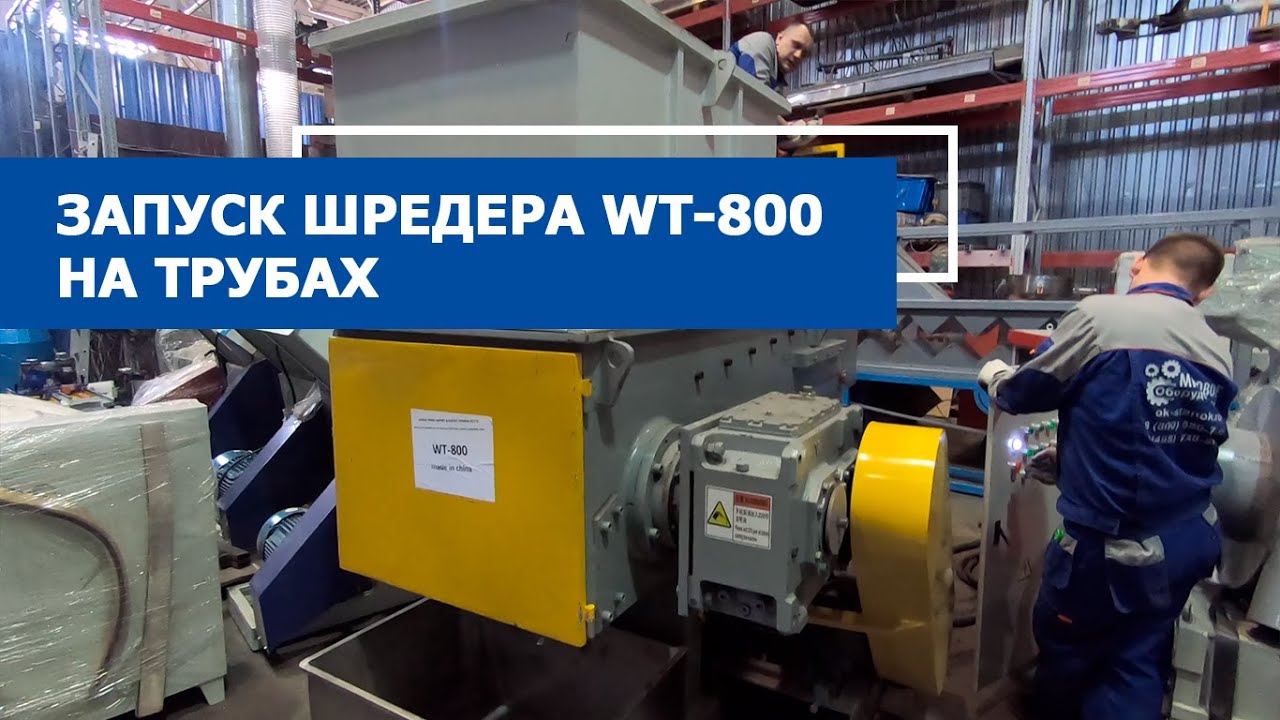
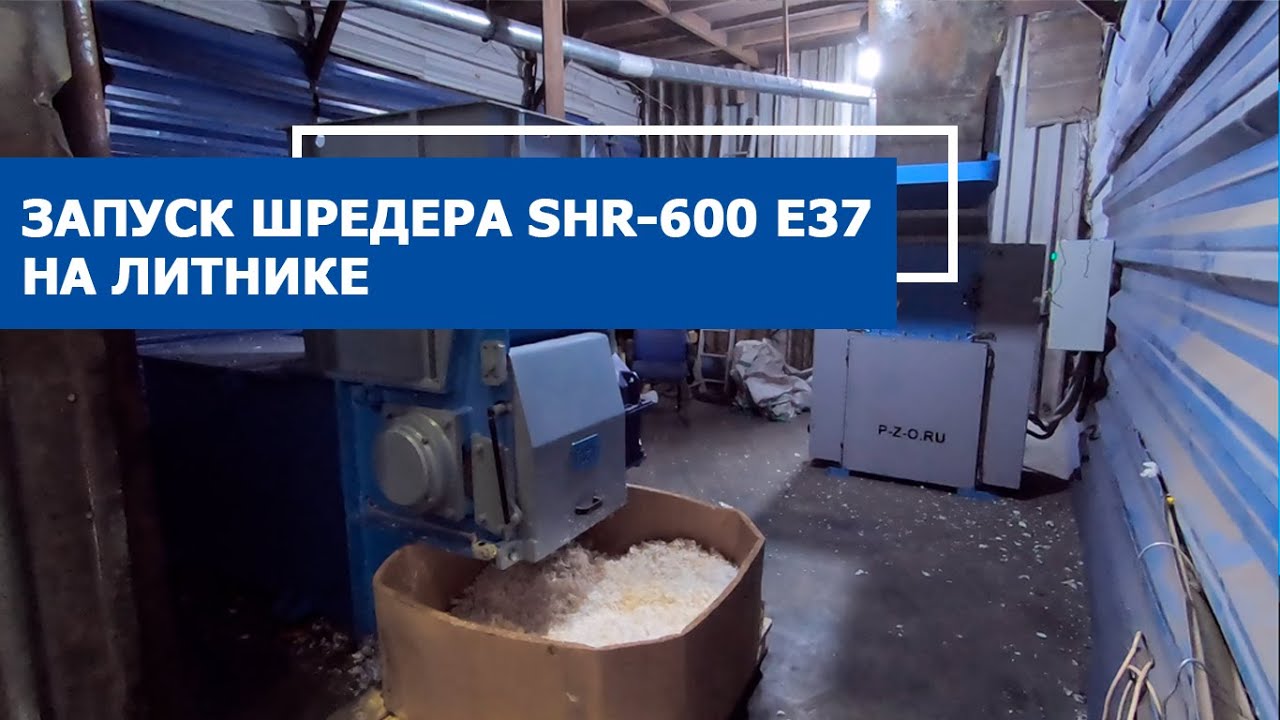
Другие видео работ вы можете посмотреть на нашем ютуб-канале по ссылке.